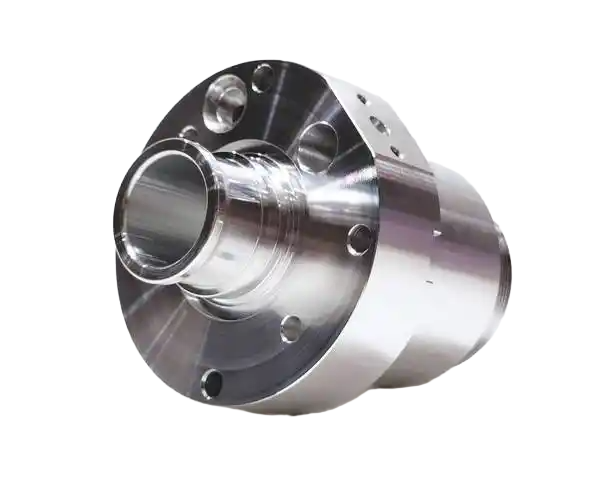
What is Press Brake Forming?
Press brake forming is a metal fabrication process that bends flat sheet metal into a final shape using a press brake machine. Force is applied between a punch (upper tool) and die (bottom tool), and linear bends can be made for a variety of metal materials and thicknesses. All brakes are equipped with CNC controllers for precise part positioning and repeatability. Press brake forming works well to create parts that include U-bends, flanges, channels, and internal bends. Lead times for qualifying formed parts are as fast as three days.
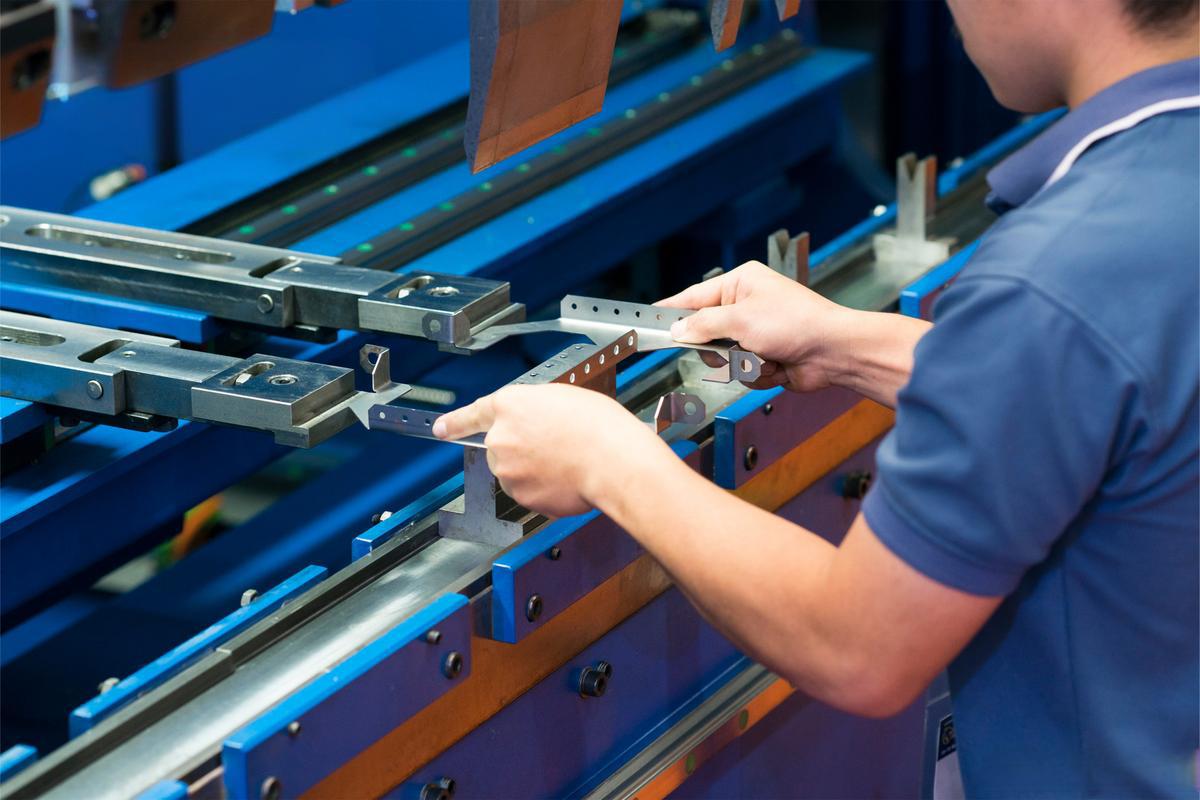
Sheet Metal Forming Design Guidelines and Capabilities
Follow these guidelines for formed sheet metal parts to ensure consistent quality and fast production times:
Maximum Bend Length |
47 in. |
Minimum Qualifying Part Size |
0.05 in x 0.05 in (12.7mm x 12.7mm) for formed parts |
Maximum Pressing Force |
80 tons |
Bend Angles |
1 degree ‘kick’ to 135 degrees |
Bending Output |
Linear bends—external and internal flanges |
Maximum U-Channel Ratio |
2:1 (width:height) |
Internal Radius Tooling Options |
0.01 in. to 1 in. (standard tooling increments) >1 in. radius bends will be bump formed |
Offsets |
Standard offset tooling sizes |
Hems |
Closed hems up to 47 in., open hems up to 36 in. |
Forming Best Practices |
|
Sheet Metal Materials and Thicknesses for Formed Parts
We offer the following metal materials for custom-formed sheet metal parts.
Note that based on material thickness, maximum bending capabilities will vary.
Material |
Grade |
Thicknesses Available |
Aluminum |
|
|
Steel |
|
|
Stainless Steel |
|
|
Copper |
|
|
Brass |
|
|
*Formed parts made out of Aluminum 6061-T6 require manual review and are not configurable during the quoting process.
Applications for Press Brake Formed Parts
Press brake forming is a commonly used manufacturing process in industries such as energy storage, computer electronics, robotics, medical, and aerospace. Common sheet metal parts fabricated with forming include:
- brackets
- busbars
- covers
- panels
- mounts
- housings or enclosures
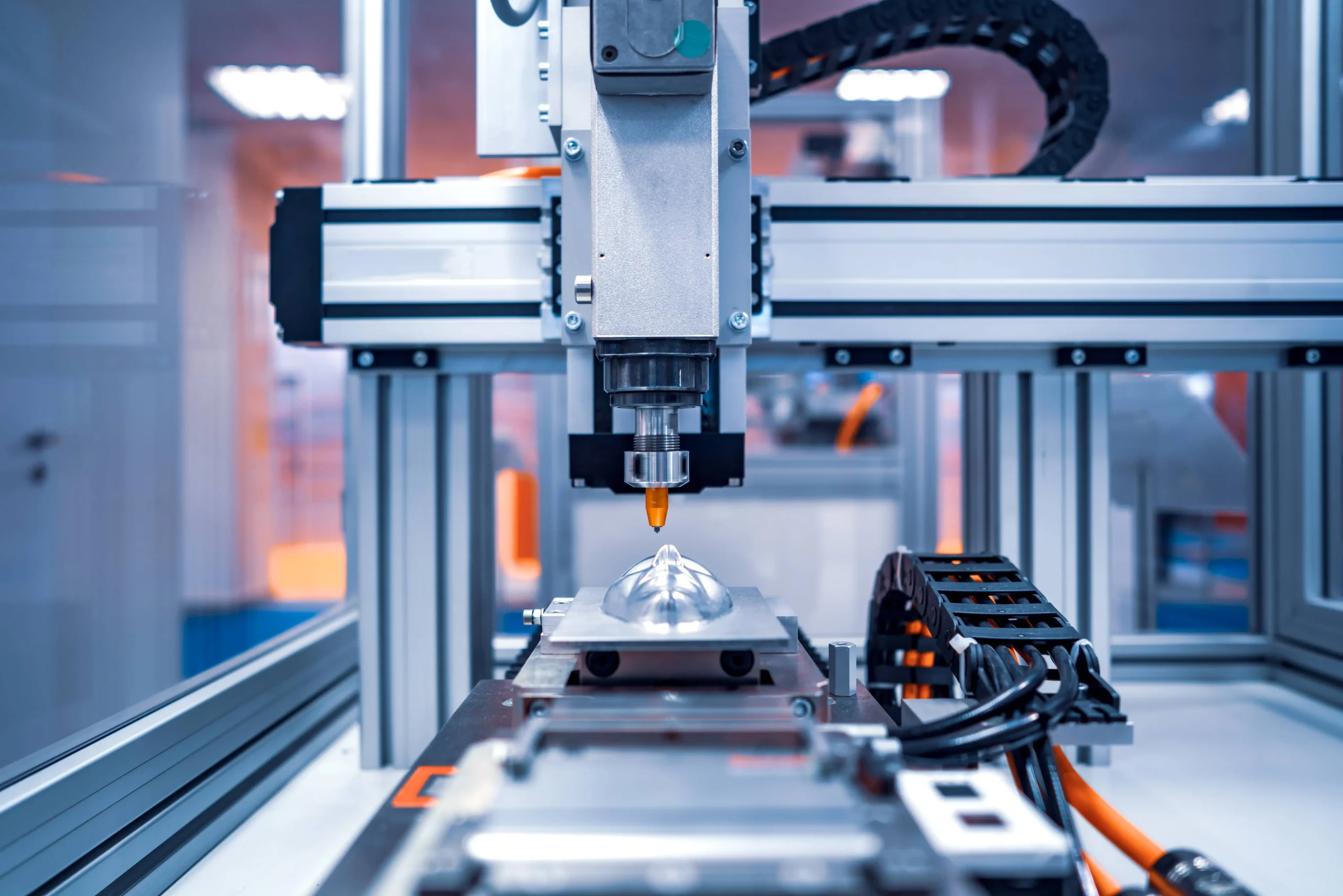