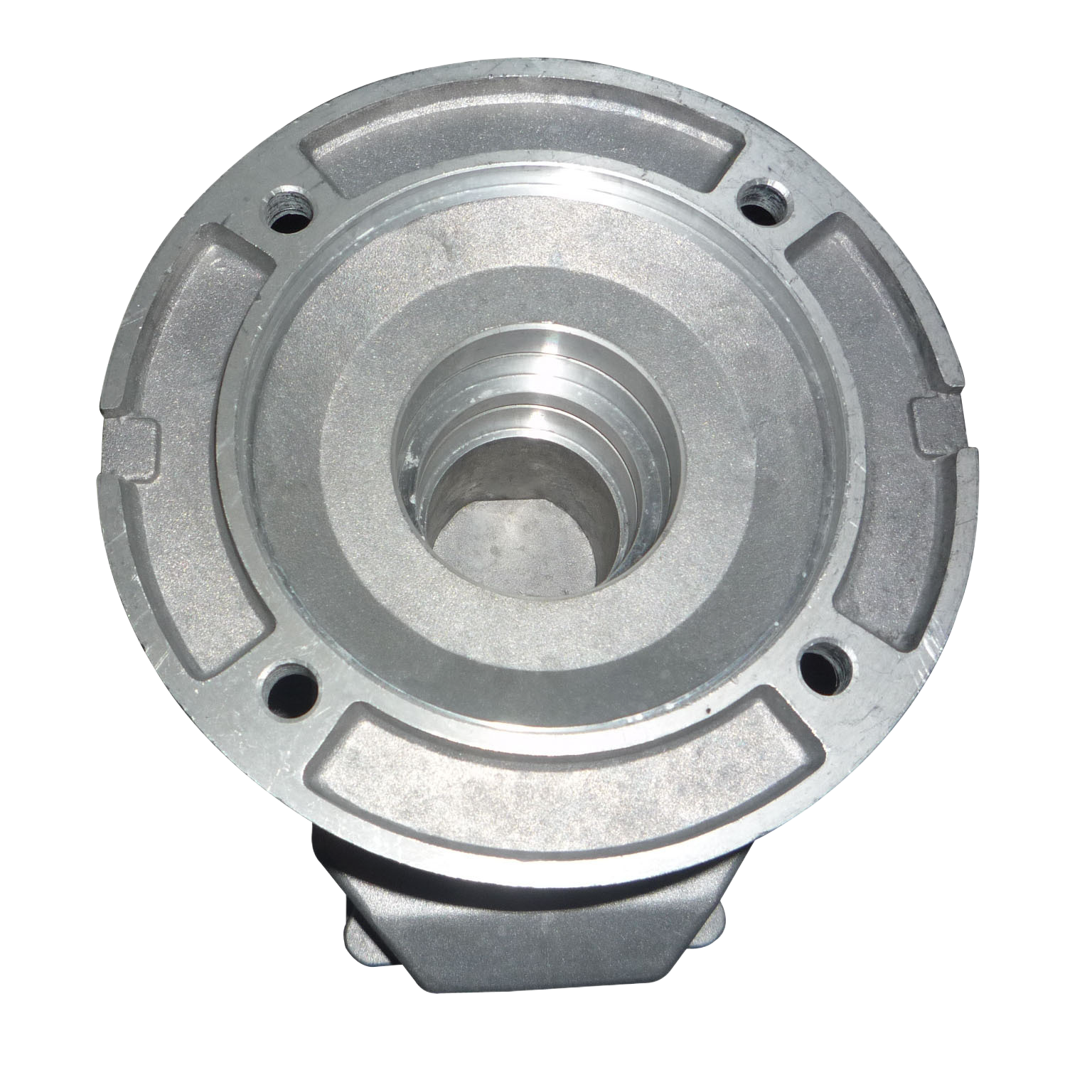
With decades of experience in the gravity casting industry, XS's gravity casting services can meet customers' needs for mass production of low-cost castings. Our factory is capable of handling custom gravity castings with simple or complex shapes, allowing for endless possibilities in gravity casting. Once you choose us, our engineers will first understand your requirements, select a gravity casting design suitable for the application, and clarify the shape, size, specifications, tolerances, and all details of the gravity casting before production. We have skilled operators in the workshop who perform each operation in the correct manner to ensure that the products meet or exceed international standards and customer expectations. Through the fast and efficient gravity casting process, we can obtain cast products that are strong, lightweight, and corrosion-resistant.
Benefits of the Gravity Casting Process
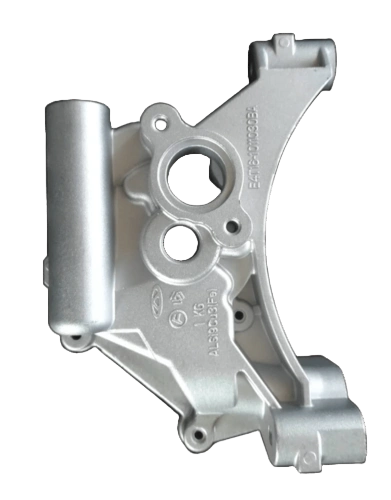
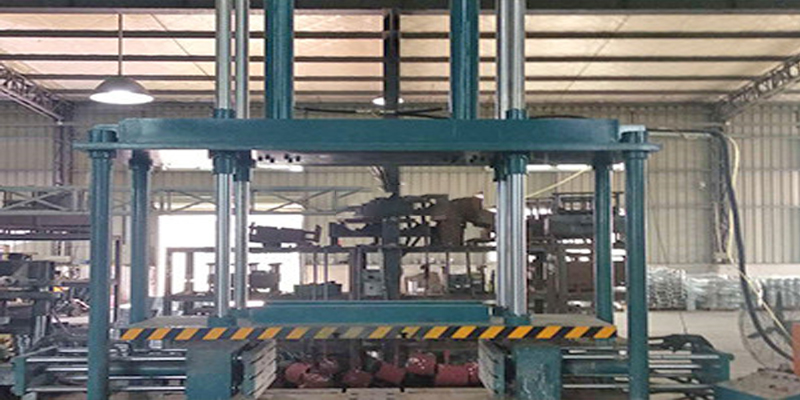
Gravity casting equipment
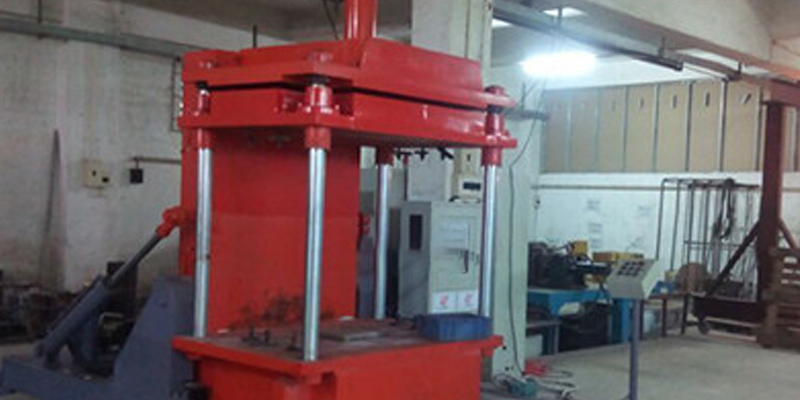
Gravity casting equipment 2

Gravity casting equipment 3
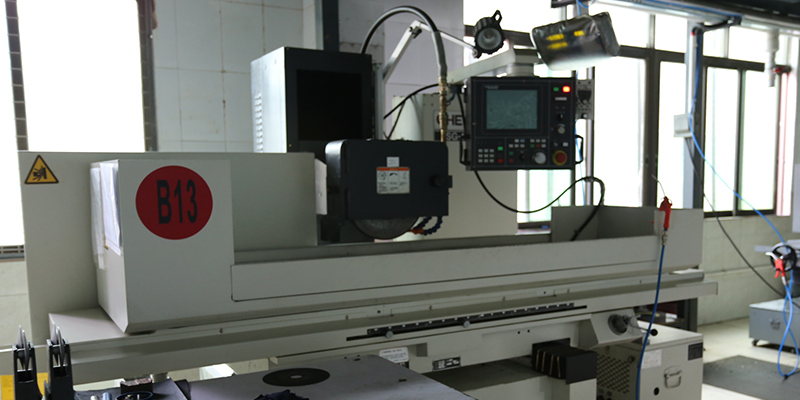
Gravity casting equipment
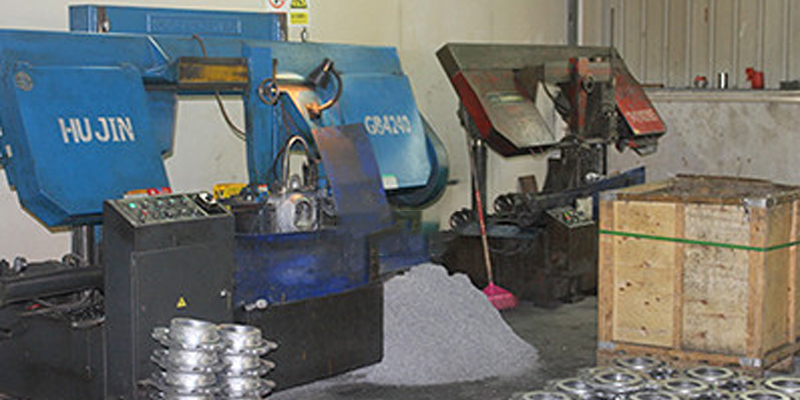
Riser cutting machine
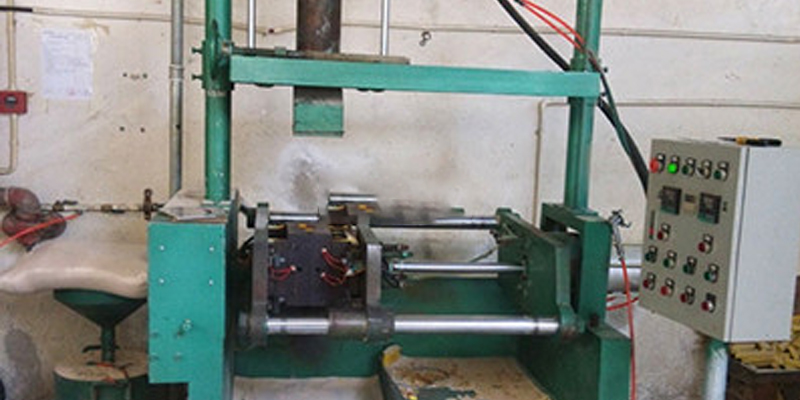
Sand core machine
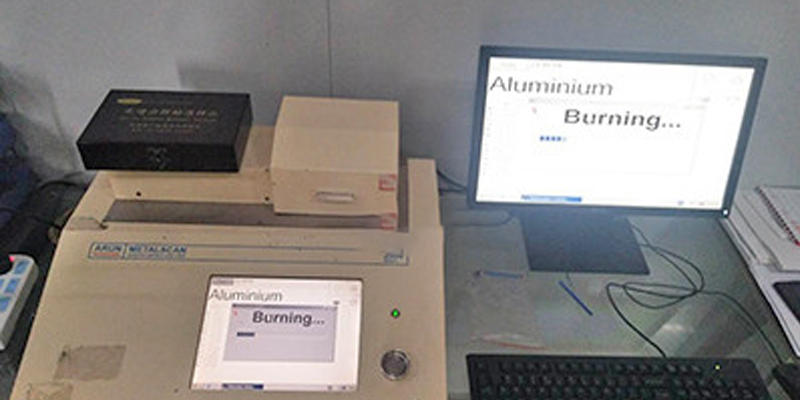
Spectrometer
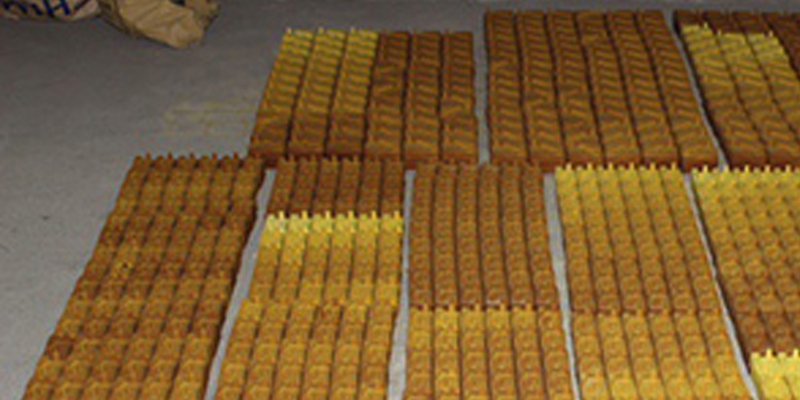
Sand core
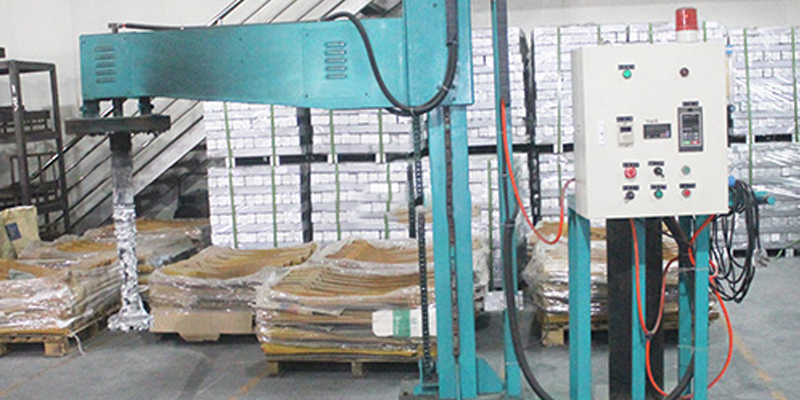
Aluminum liquid refining machine
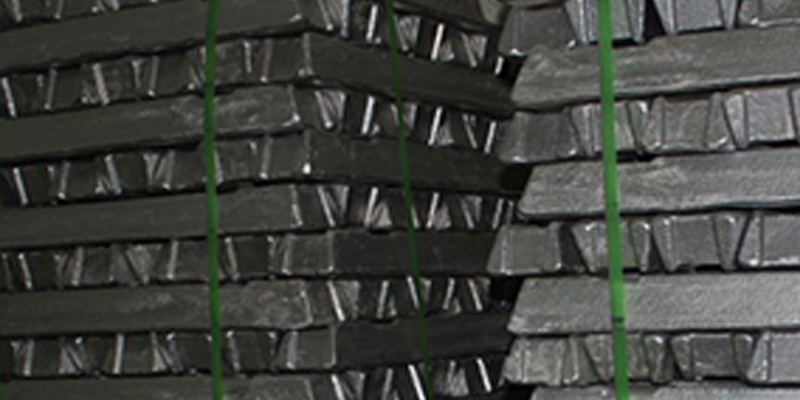
Aluminum ingot
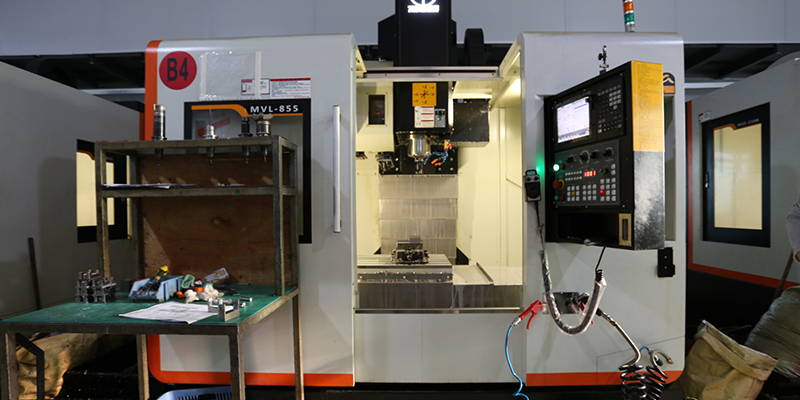
CNC machine tool
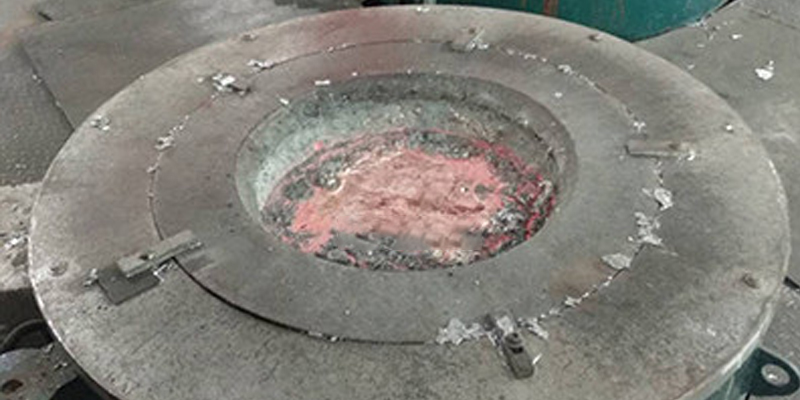
Electric oven
XS Gravity Casting Cases
XS manufacturing services can be applied to the actual design and small-batch production runs of die castings, sand castings, investment castings, metal castings, lost foam castings, etc.
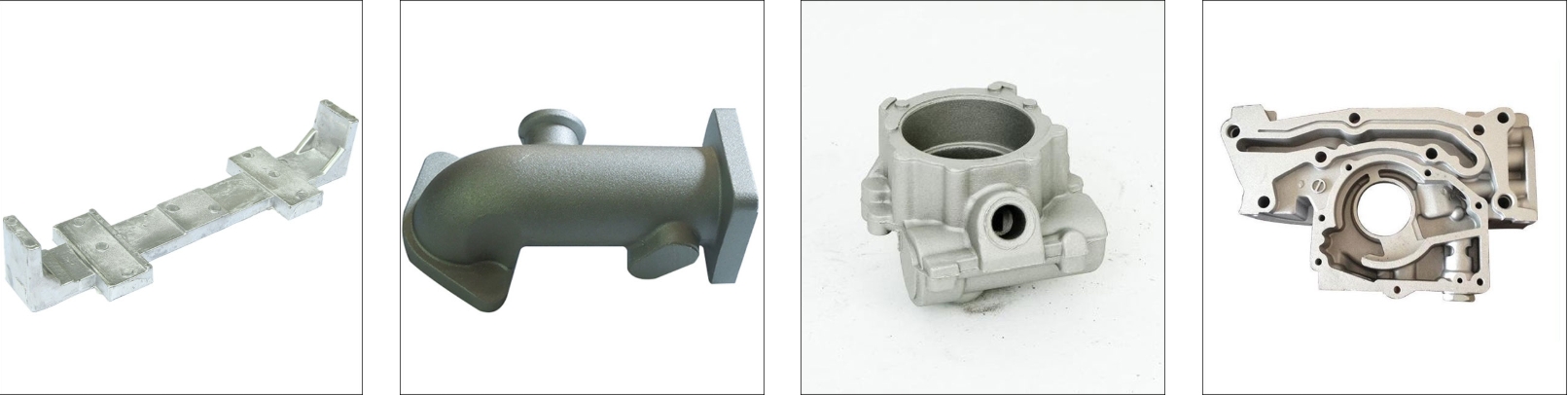
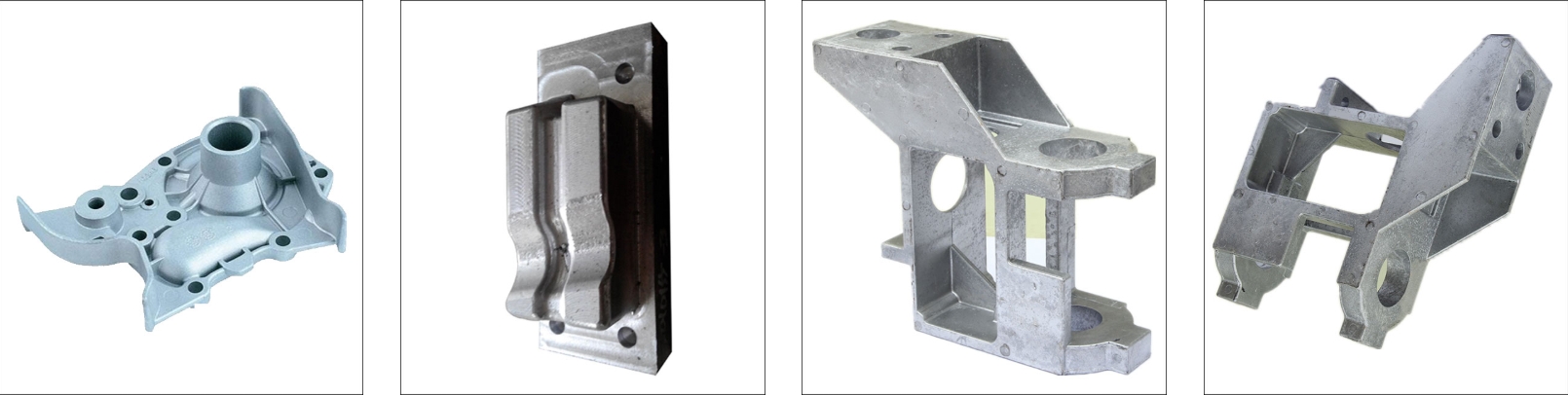