Thin-Wall Die Casting
Aluminum alloys, characterized by light weight and excellent mechanical properties, show great prospects in the production of large and complex structures such as vehicle bodies and automobile chassis.
Certifications ISO 9001:2015 | CTQ Inspections | ISO 13485
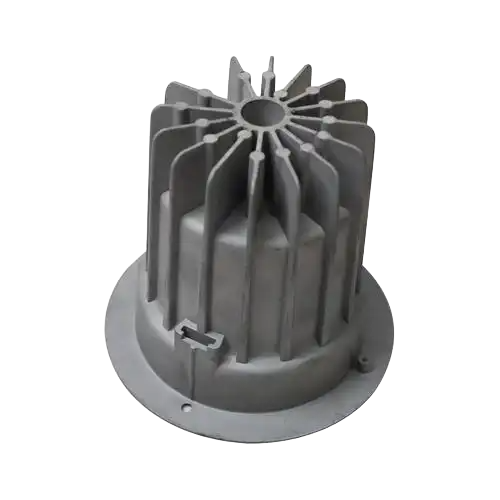
What is Thin-Walled Die Casting?
Industries such as aerospace, automotive, and ordnance, in pursuit of rational part structures and lightweight designs, have replaced assemblies of simple castings, forgings, and machined parts with integral castings. Non-ferrous alloy castings with a wall thickness of 2.0–4.0mm are called thin-walled castings, while aluminum alloy castings with a wall thickness of less than 2.0mm are referred to as ultra-thin-walled castings.
As a rapid near-net-shape process, die casting offers advantages such as high production efficiency, high dimensional accuracy, and the ability to form complex-shaped, sharply contoured thin-walled and deep-cavity castings. It is particularly suitable for the integrated design and integral forming of thin-walled complex parts.
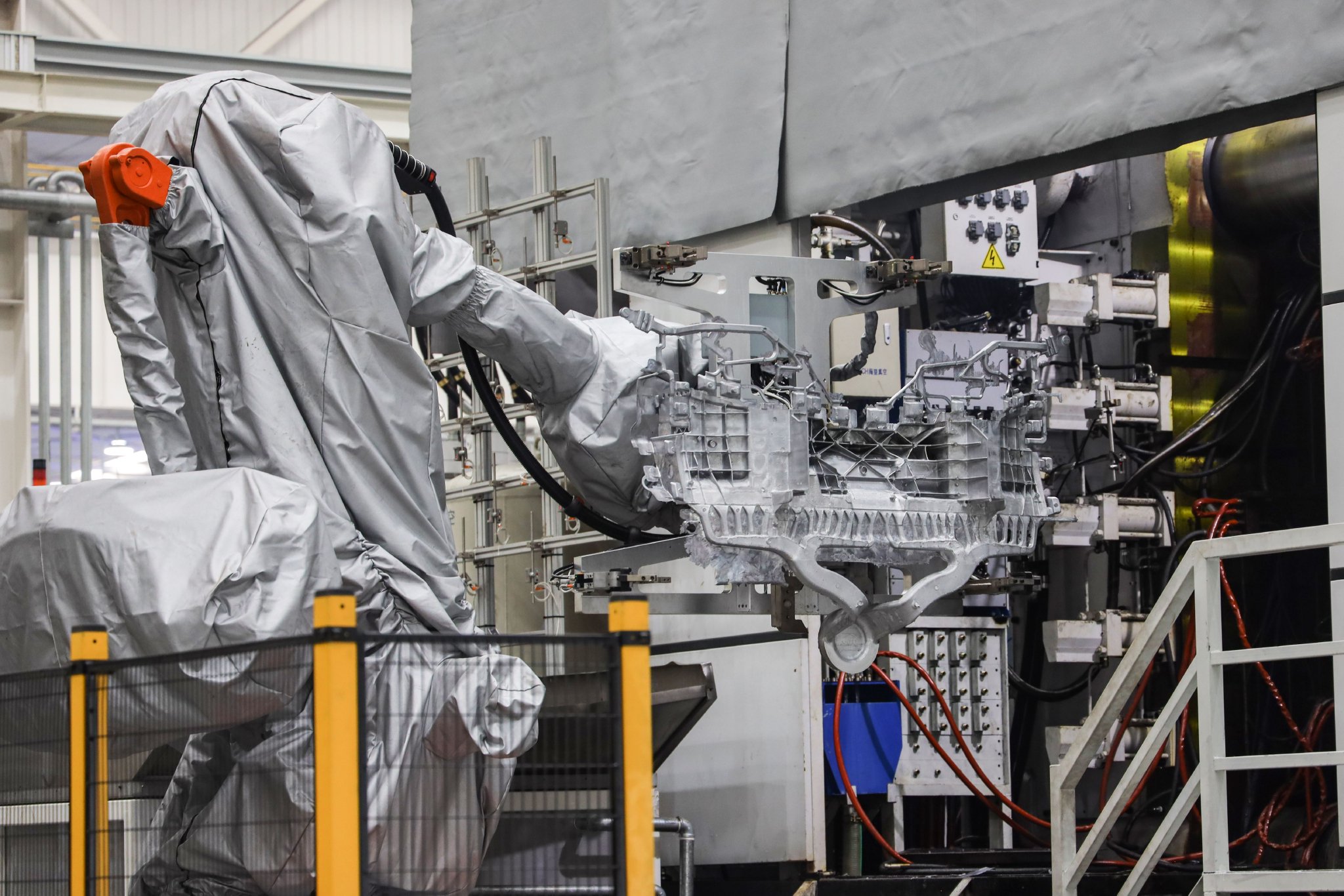
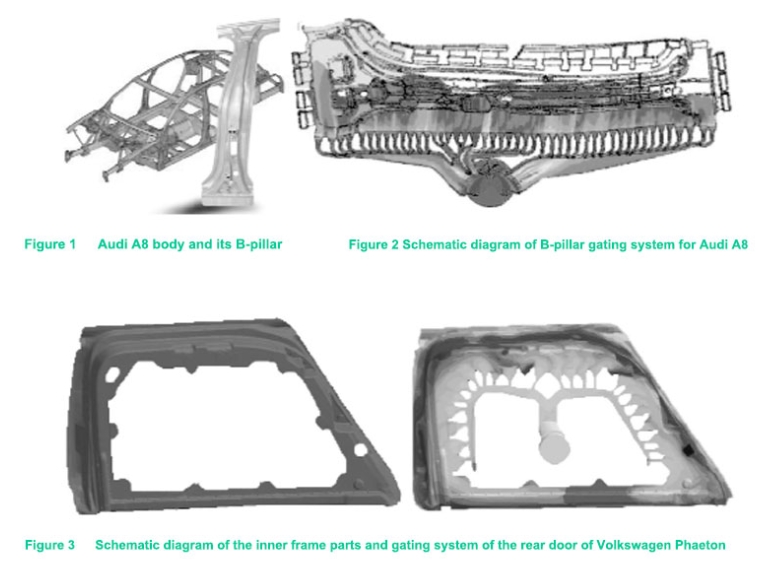
Aluminum alloy thin-walled die castings are mainly used in the body and chassis of high-end automobiles. Figure 1 shows the aluminum alloy space frame structure of the Audi A8 body. The B-pillar is the casting with the largest size, the most complex shape, and the highest mechanical performance requirements. Its outer dimensions are approximately 1200 mm × 200 mm × 100 mm, with a wall thickness of 1.0–2.5 mm. Figure 2 is a schematic diagram of its gating system.
It can be seen from Figure 2 and Figure 3 that this gating system adopts a multi-slot ingate method, and is assisted by a vacuum system. A mold temperature controller is required to control the mold temperature, and the casting needs to undergo special heat treatment to meet the final service requirements. However, the specific process parameters of vacuum die casting and heat treatment are confidential.
Die casting materials
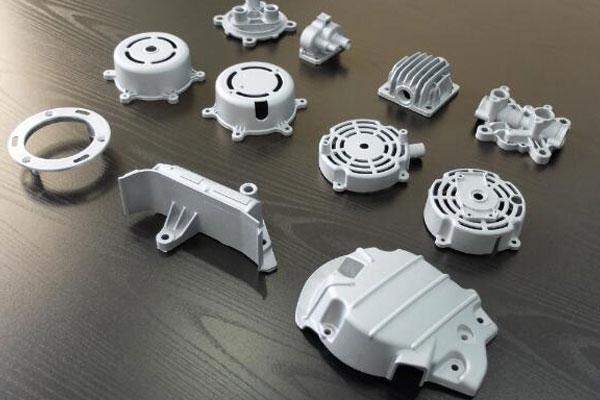
Aluminum Die Castings
- A360
- A380
- ADC6
- ADC10
- ADC12
- Aluminum-Silicon 12 (Al-Si12)
- Aluminum-Silicon 9Cu3 (Al-Si9Cu3)
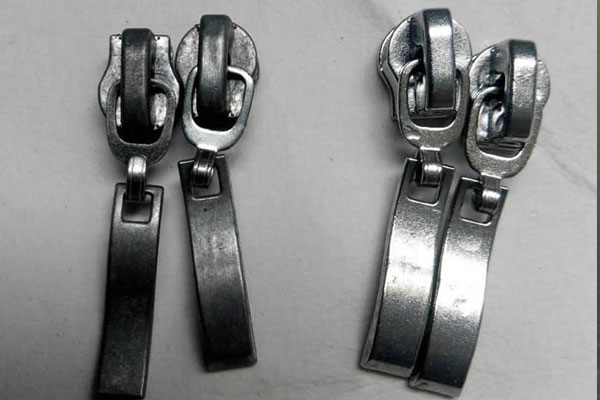
Zinc Die Castings
- Zamak 3
- Zamak 5
- Zamak 8
- Zamak 12
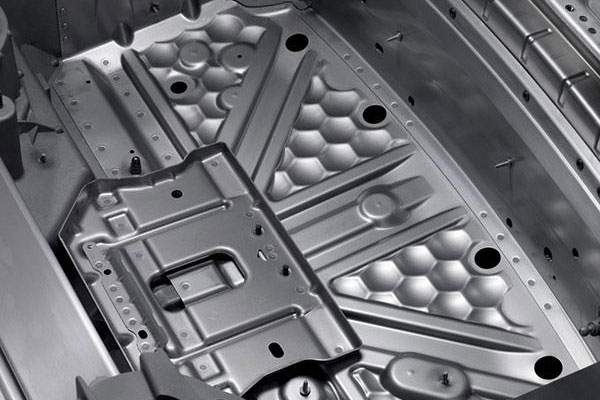
Magnesium Die Castings
- AM50A
- AM60B
- AZ91D
- AZ63A

Other Casting Materials
- Titanium
- Copper
- Bronze
- Iron Plate
- Stainless Steel
- Cast Iron
Advantages of Thin-Walled Die Castings
- Complex part shapes can be achieved, enhancing part performance. Additionally, assembly work is reduced.
- Durable and dimensionally stable die castings with specific shapes can be produced, eliminating or minimizing the need for machining.
- Die castings can undergo various finishing techniques and surface treatments. The process enables the achievement of smooth or textured part surfaces.
- Net-shape part configurations can be realized.
- High dimensional accuracy can be achieved.
- Rapid production is possible.
- Thinner wall thicknesses can be achieved compared to investment casting.
- A wide range of possible shapes is available.
- External threads can be cast.
- Holes can be cored according to the size of internal thread drills.
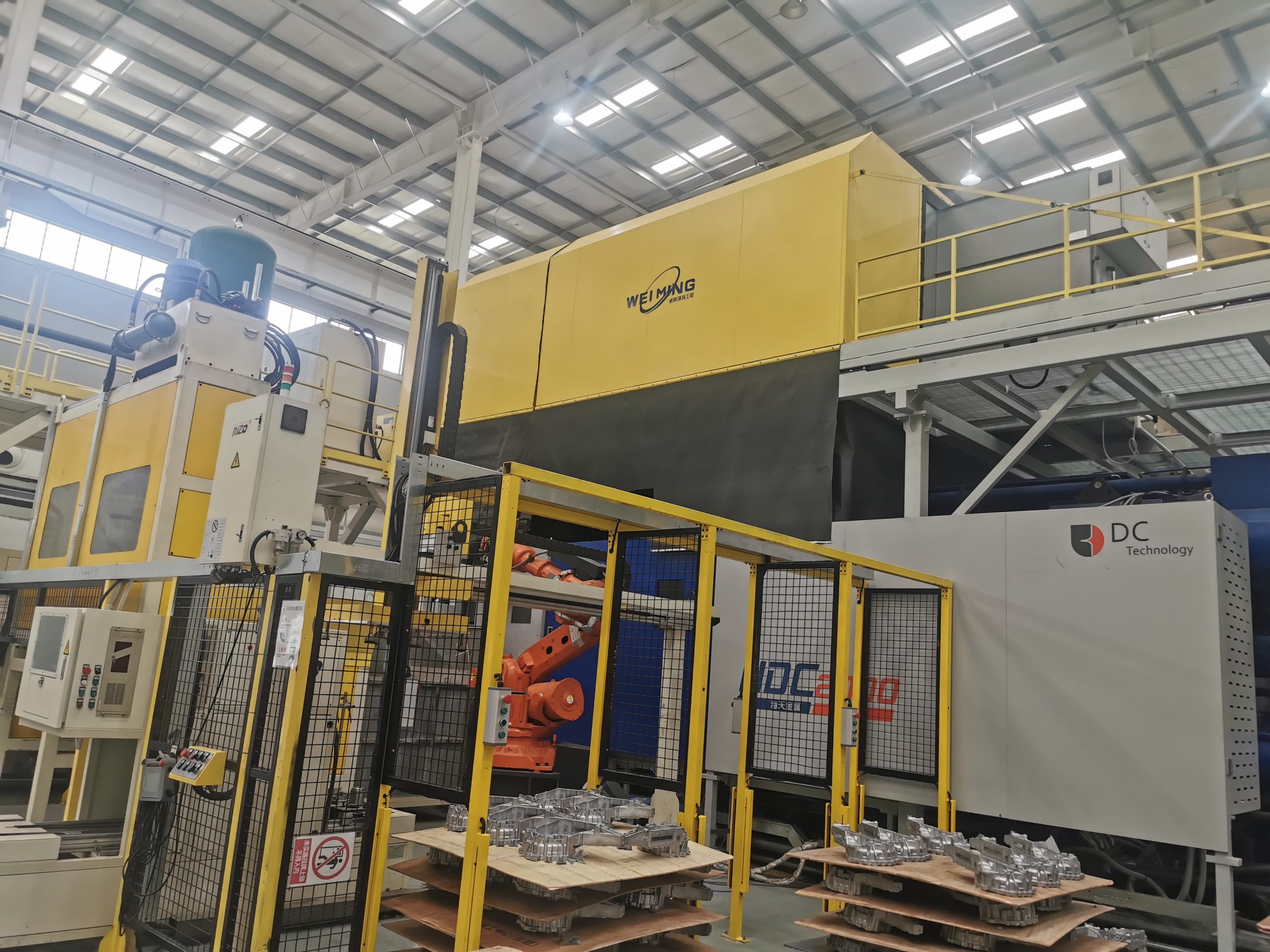