Hot Chamber Die Casting
ntegration of metal melting and die casting, with a short process and high efficiency, suitable for low-melting-point alloys such as zinc and magnesium.
Certifications ISO 9001:2015 | CTQ Inspections | ISO 13485
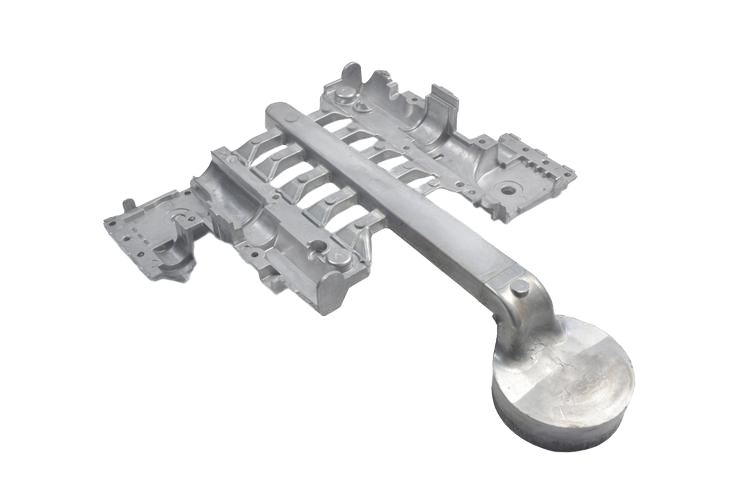
What is Hot Chamber Die Casting?
Hot chamber die casting refers to a process where the pressure chamber is immersed in the liquid metal within a heat-insulated melting crucible. The injection unit is not directly connected to the base but is mounted on the crucible. This method offers advantages such as a simple production process, high efficiency, low metal consumption, and process stability. However, the prolonged immersion of the pressure chamber and injection plunger in the liquid metal shortens their service life and may increase the iron content of the alloy.
The injection chamber is connected to the gate of the die casting mold via a gooseneck. This technique is suitable for die casting non-ferrous alloy parts with low melting points, such as zinc and lead, and is widely used in industrial sectors including automotive and motorcycle components, instruments, household hardware, and home appliances.
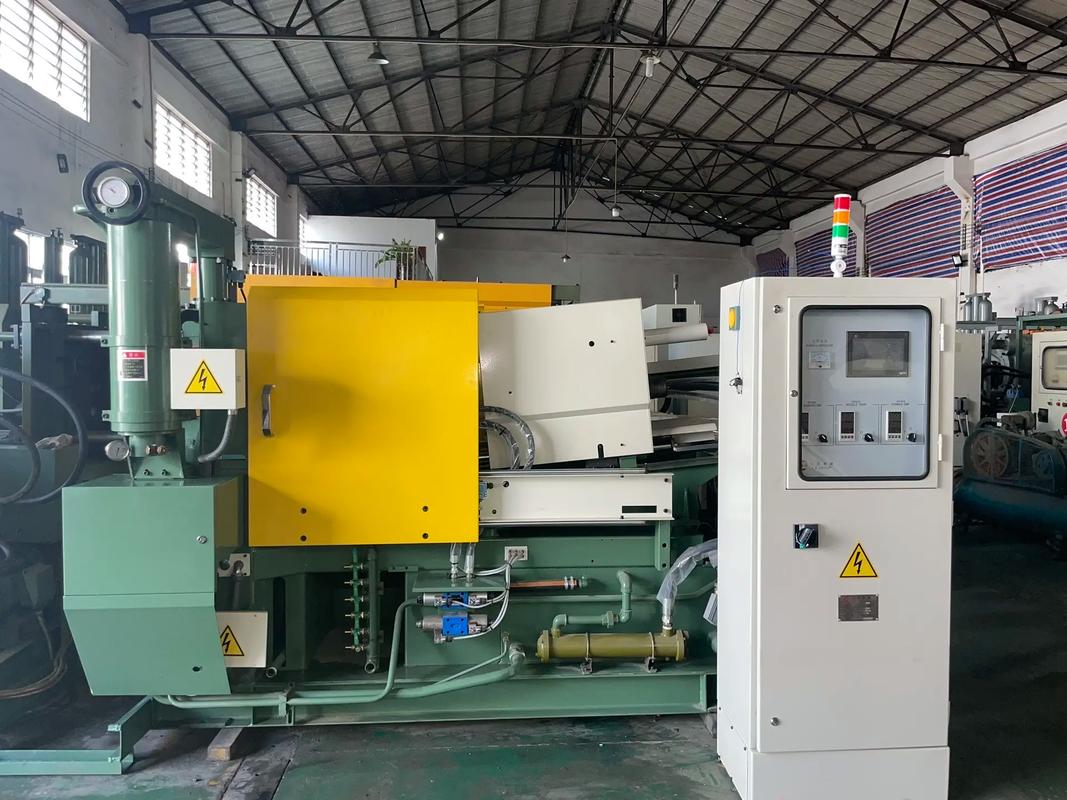
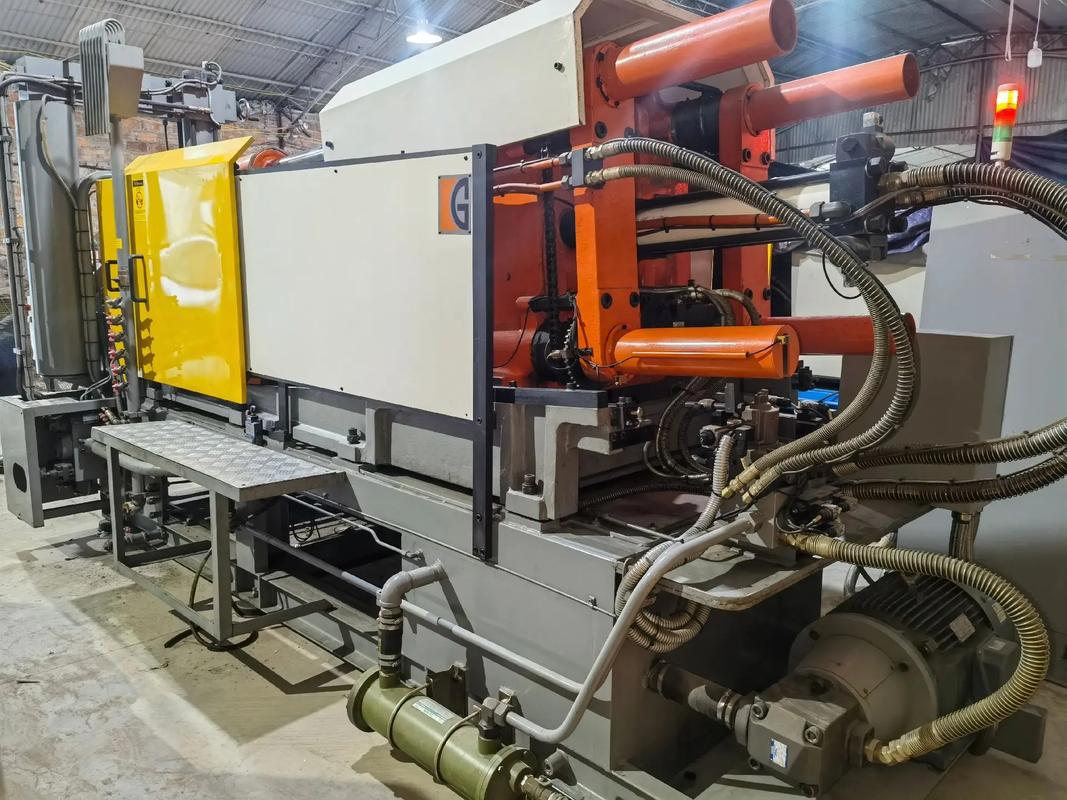
XS Hot Chamber Die Casting Services
- Easy for mass production – Since die casting is done with die casting molds, parts can be produced within specified tolerances and shapes. Little to no machining is required, and thousands of identical castings can be made before additional tooling is needed. Thus, it is easy to carry out mass production.
- Dimensional accuracy and stability – Parts produced by die casting are durable and dimensionally stable while maintaining tight tolerances. They also have heat resistance.
- Strength and weight – Die castings are stronger than injection-molded parts of the same size. Thin-walled castings are stronger and lighter than those made using other casting methods. Additionally, because die castings are not composed of separate components welded or fastened together, their strength depends on the alloy rather than the joining process.
Advantages of Hot Chamber Die Casting
- Complex part shapes can be achieved, enhancing part performance. Additionally, assembly work is reduced.
- Durable and dimensionally stable die castings with specific shapes can be produced, eliminating or minimizing the need for machining.
- Die castings can undergo various finishing techniques and surface treatments. The process enables the achievement of smooth or textured part surfaces.
- Net-shape part configurations can be realized.
- Complex casting details can be achieved.
- Reduced porosity.
- Longer die life due to lower melting points.
- Efficient mold design = reduced waste.
- Fast cycle times (approximately 15 cycles per minute).
- Convenience in melting metal during the casting process.
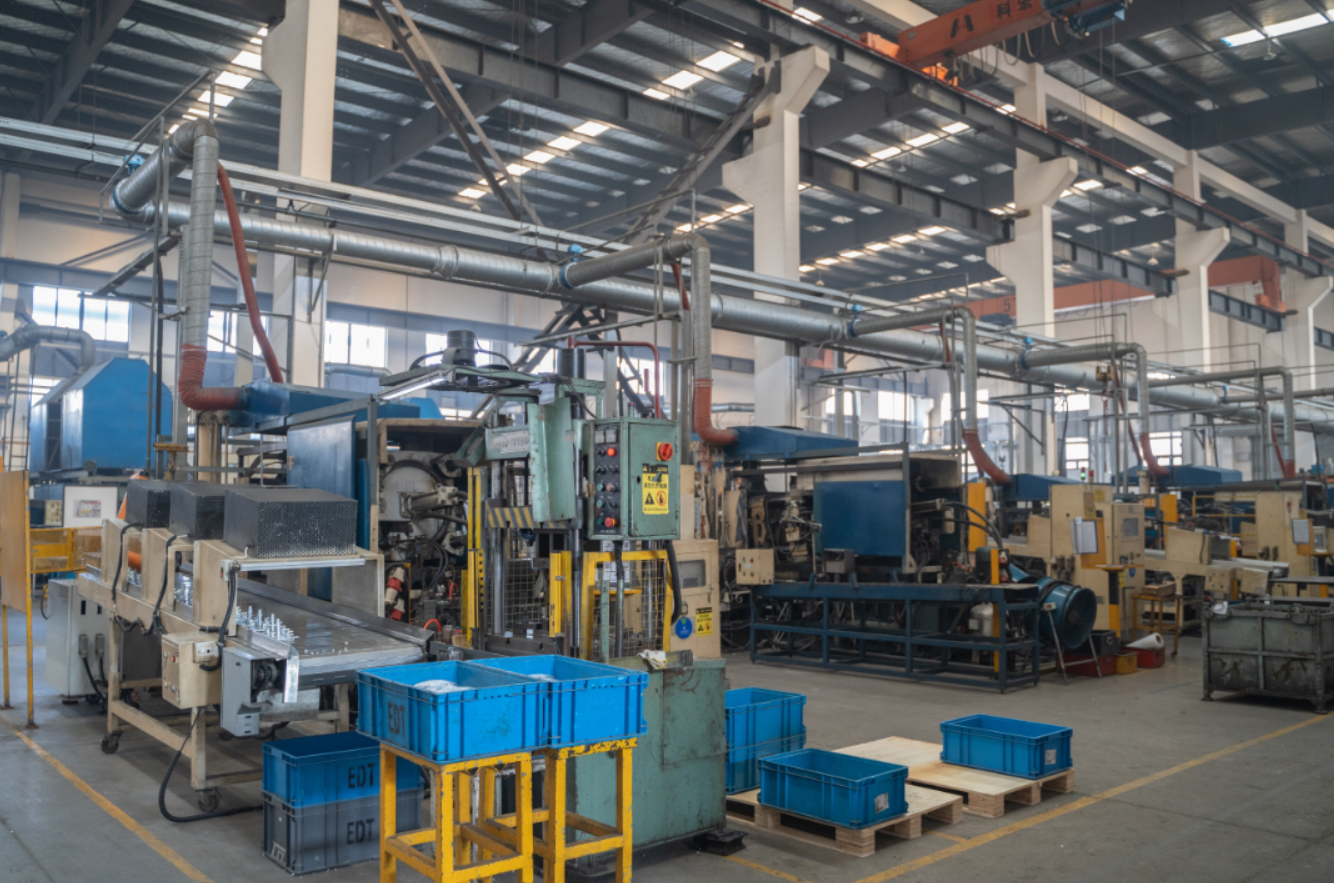
Hot Chamber Die Casting Cases
If you have a complex part design, XS can help turn it into reality. With suitable equipment, strong technical expertise, and a focus on quality, we ensure every project is completed to high standards—from tooling design and finishing to shipping—and guarantee your orders are delivered on time, every time.
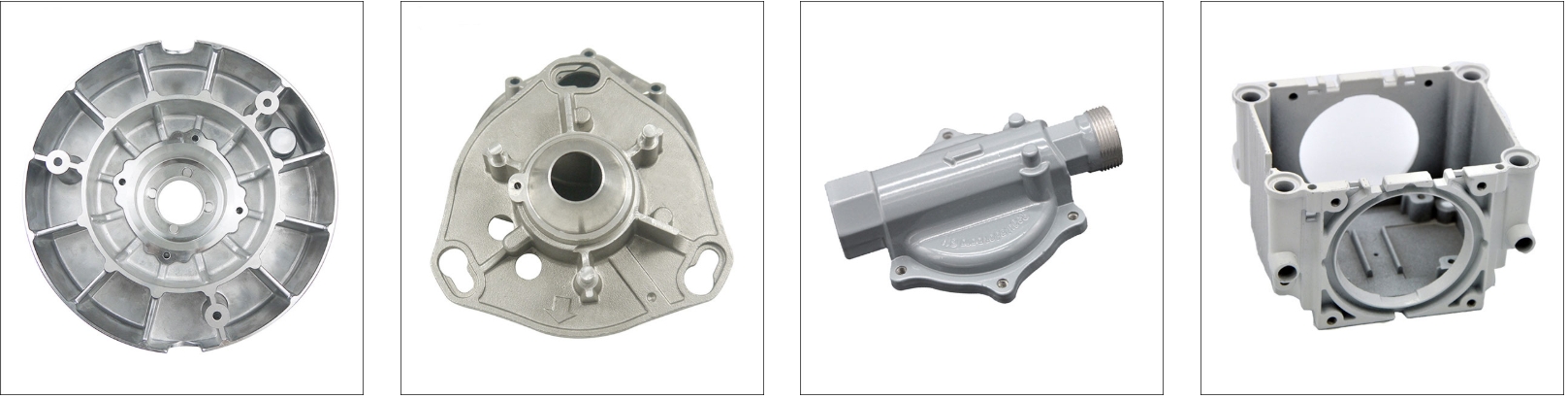
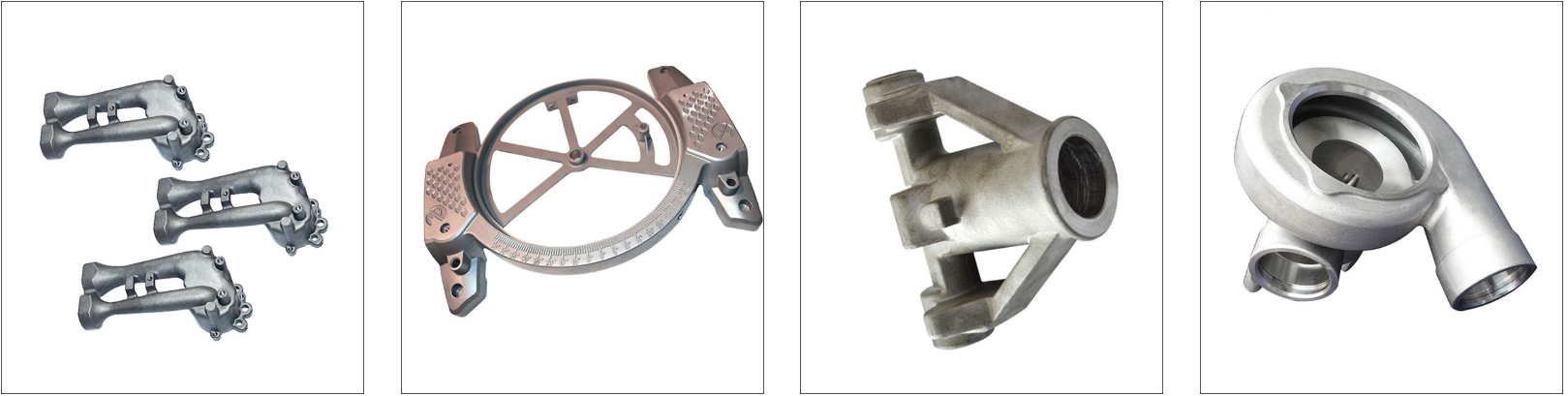
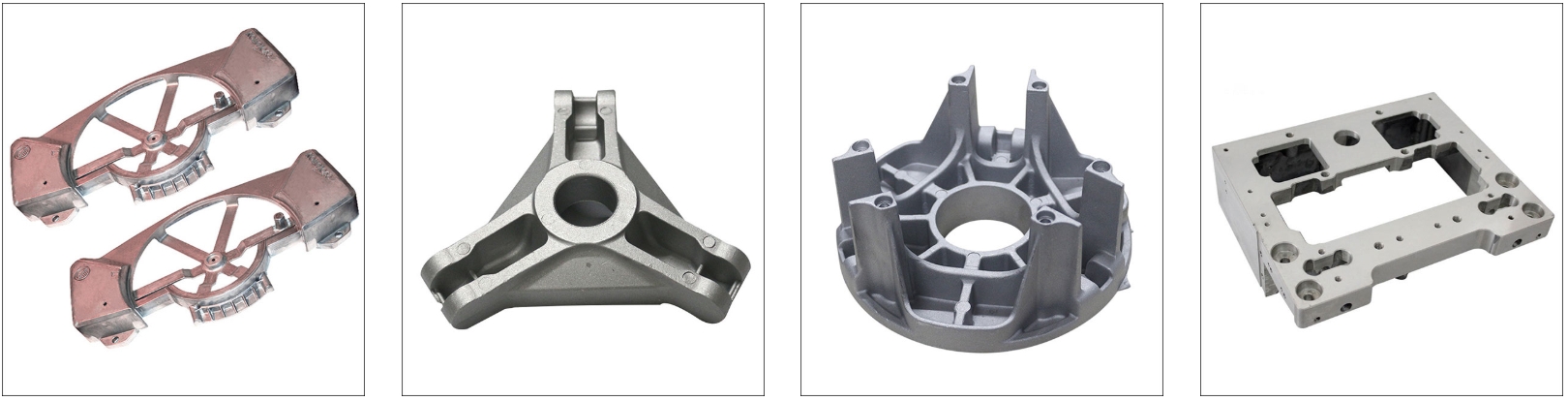