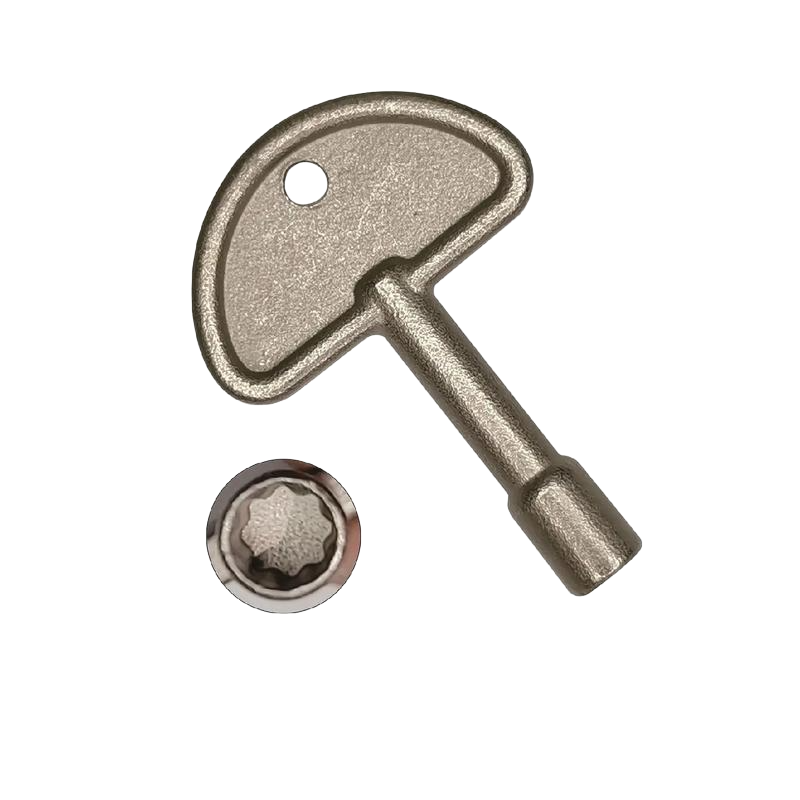
Lost wax casting involves making a wax pattern of the part to be cast using wax, and then coating the wax pattern with slurry to form a clay mold. After the clay mold dries, it is placed in hot water to melt the internal wax pattern. The clay mold is taken out from the melted wax pattern and fired into a ceramic mold, which is fired once. Generally, a sprue is left when making the clay mold, and then molten metal is poured through the sprue. After cooling, the required part is produced.
Materials used in lost wax casting:
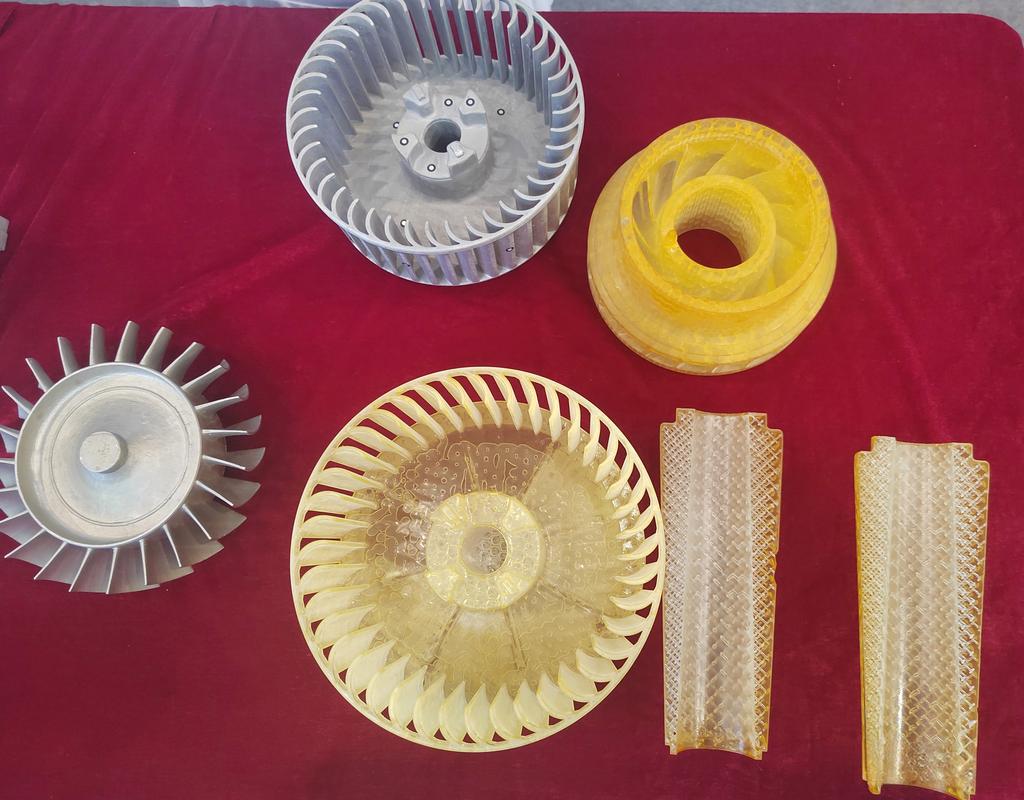
Benefits of Lost Wax Casting Process
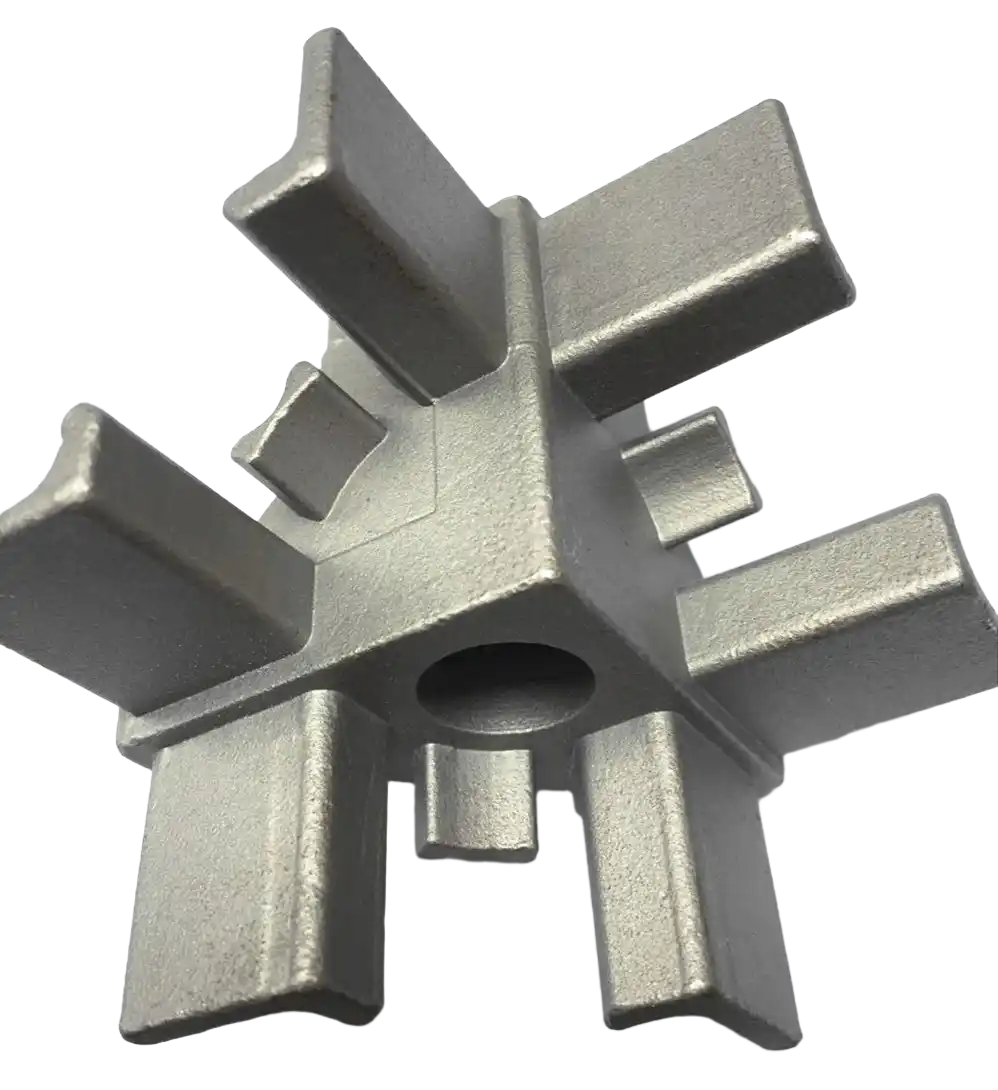
Lost Wax Casting Hardware Processing Technology
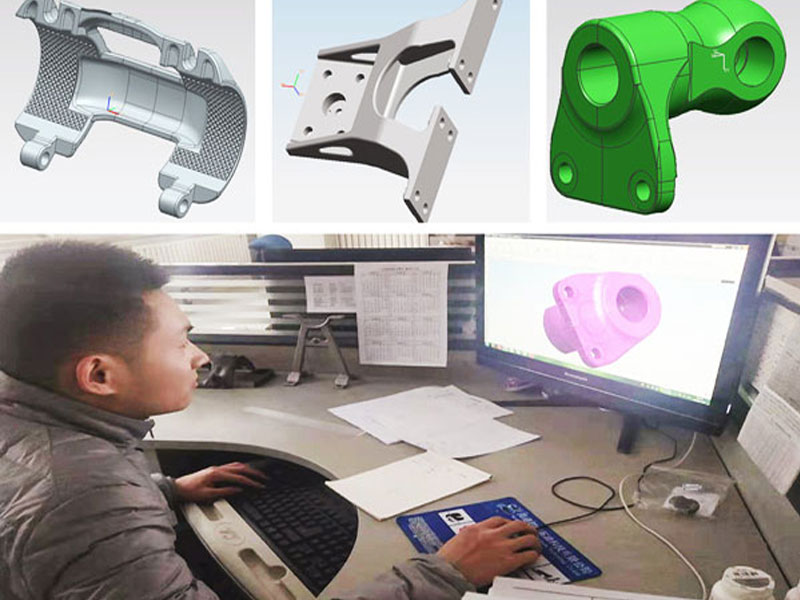
Mold development and design
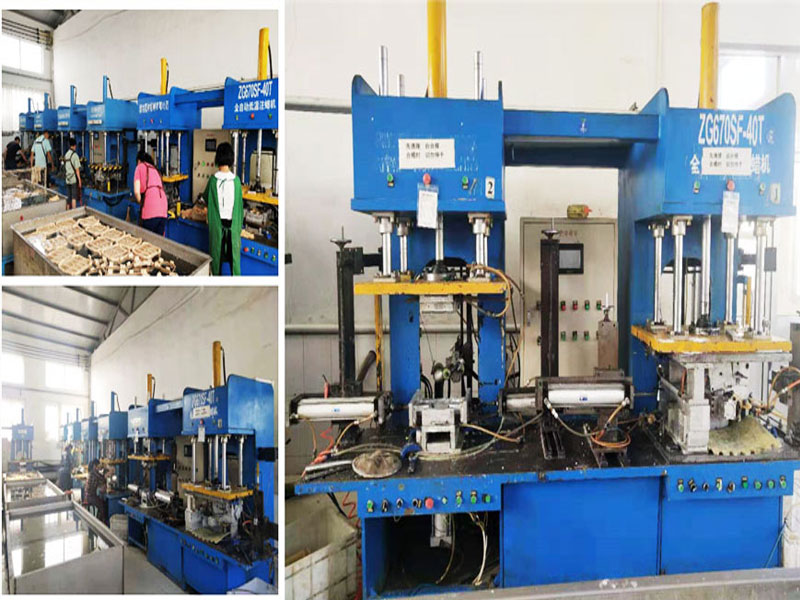
Lost wax workshop
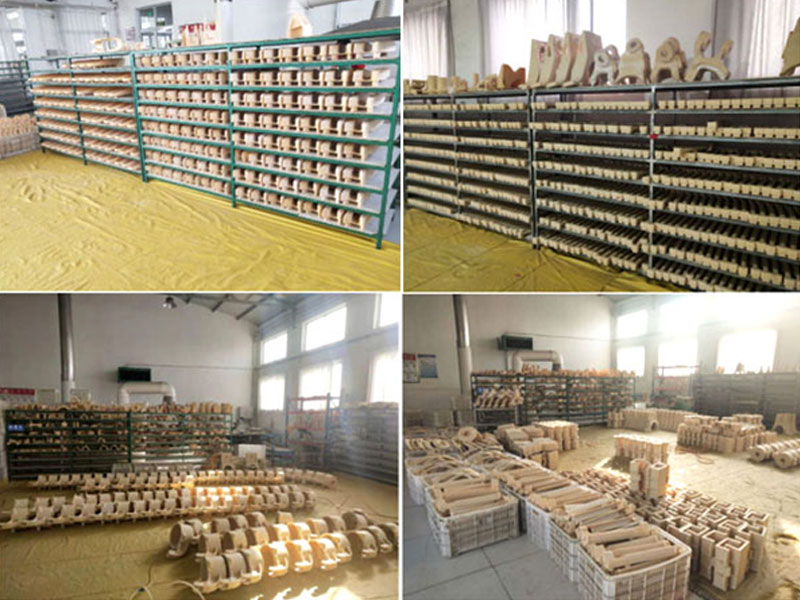
Lost wax inspection
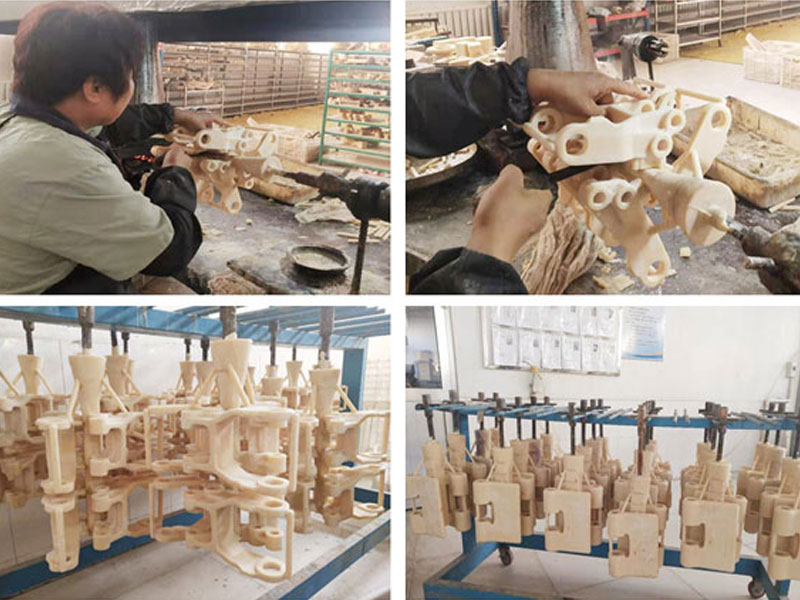
Wax pattern assembly (tree grouping)
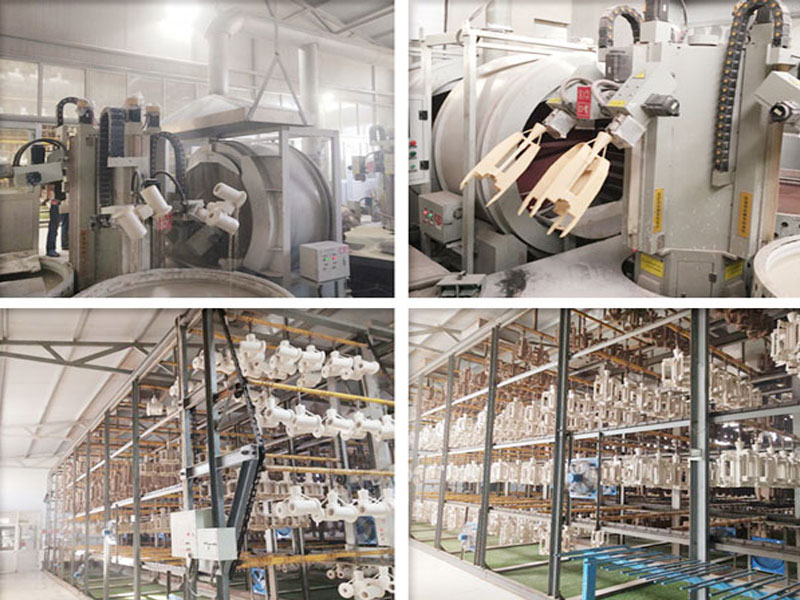
Silica sol shell
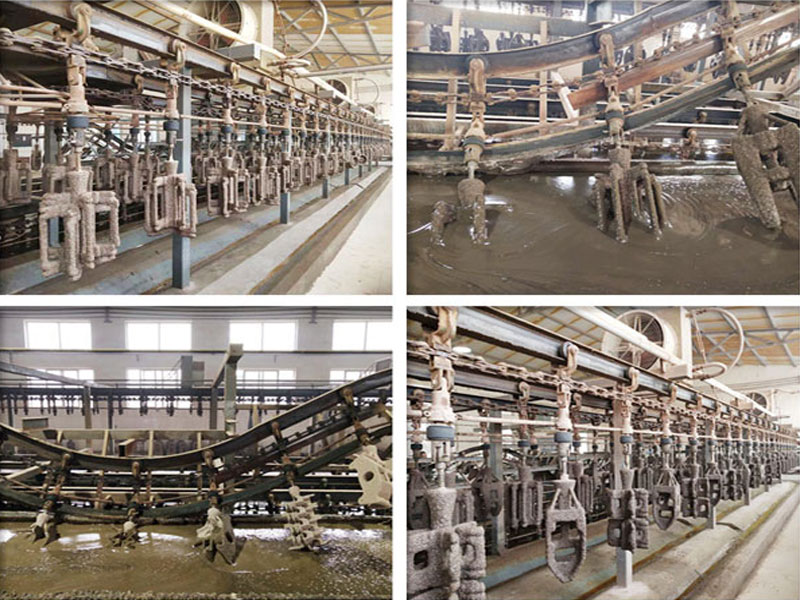
Water glass reinforcement
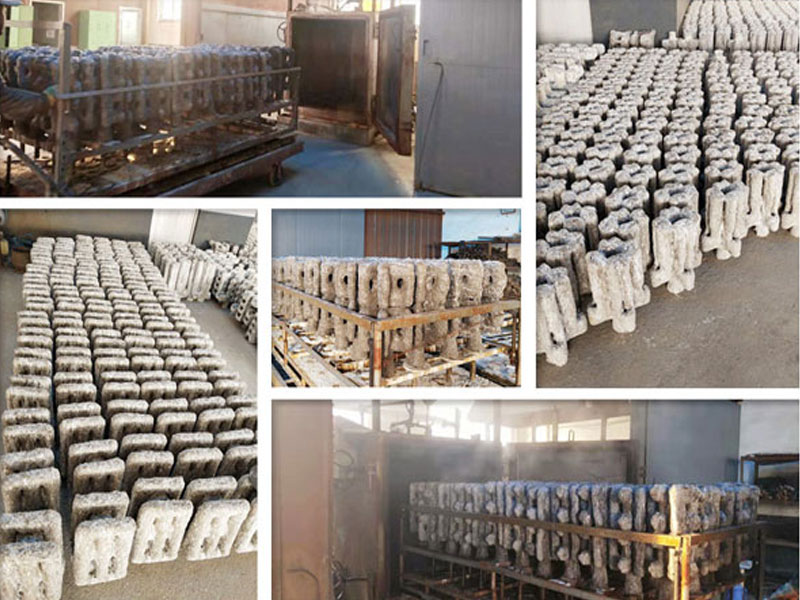
Steam dewaxing
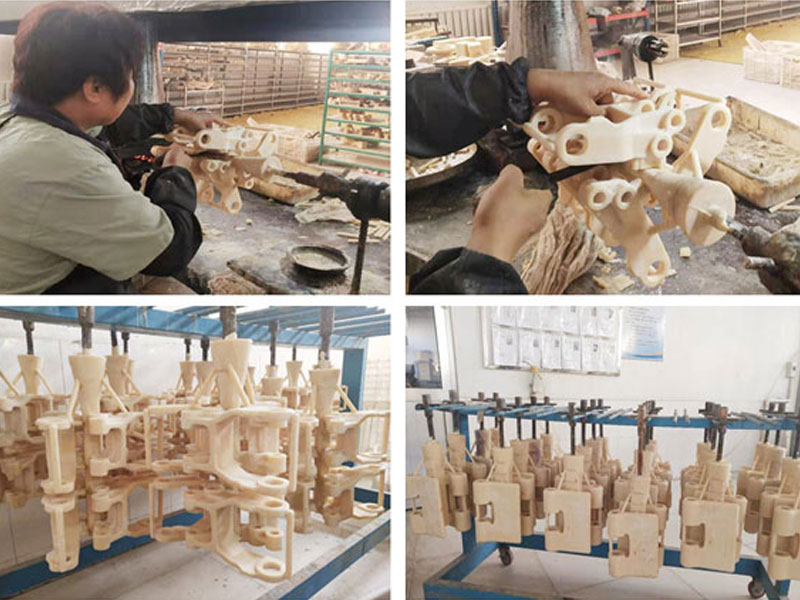
Roasting and pouring
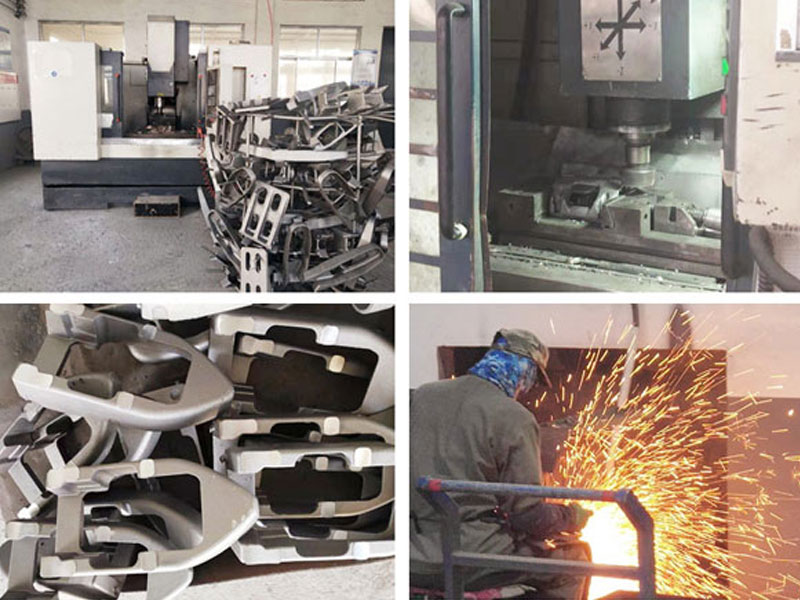
Gate removal and grinding
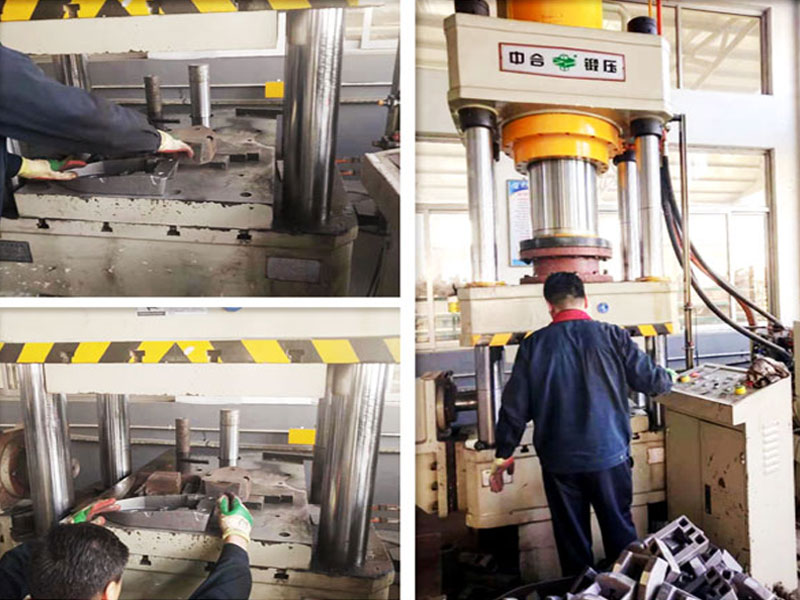
Correction
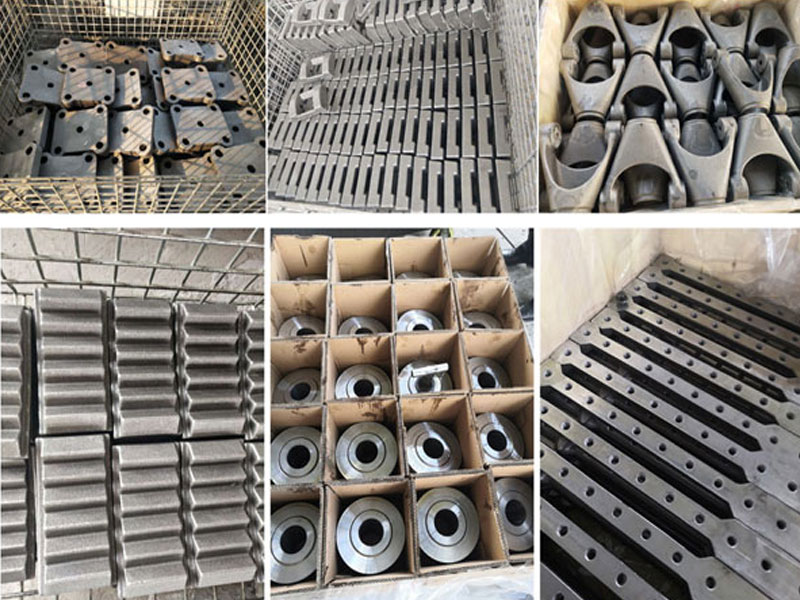
Complete precision castings
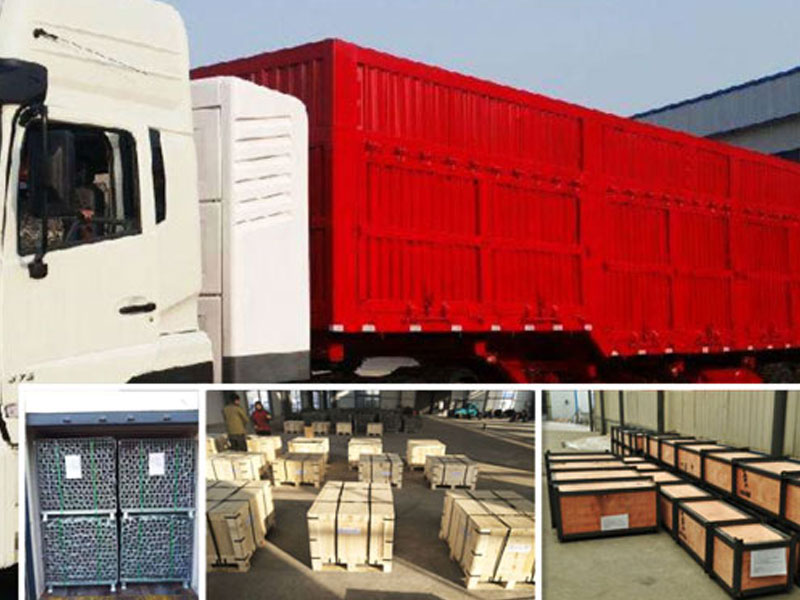
Packaging and shipping
Lost wax casting cases
XS manufacturing services can be applied to your die castings, sand castings, investment castings, metal castings, lost foam castings, etc.
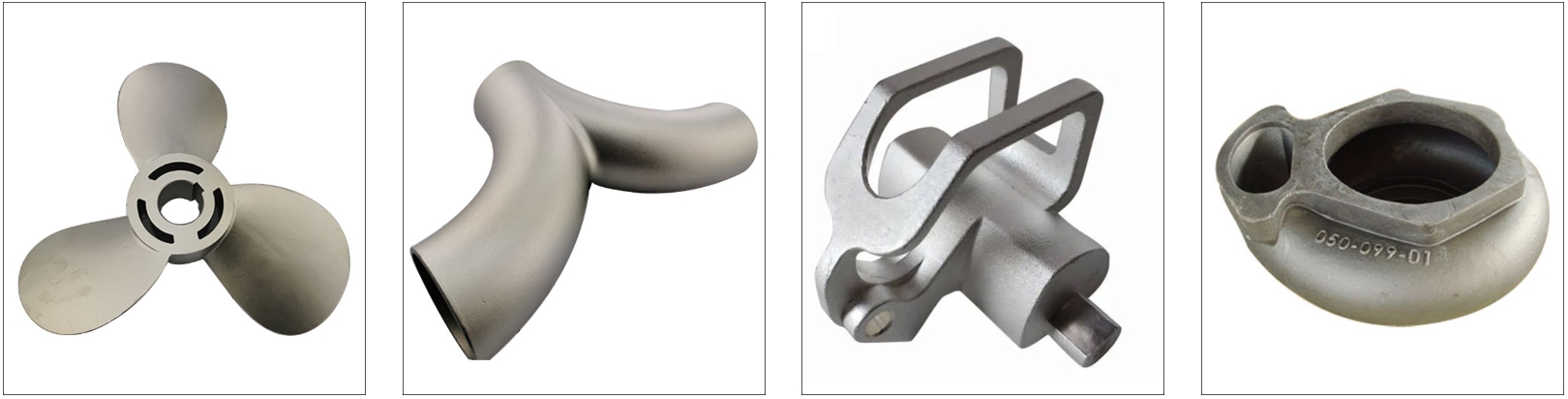
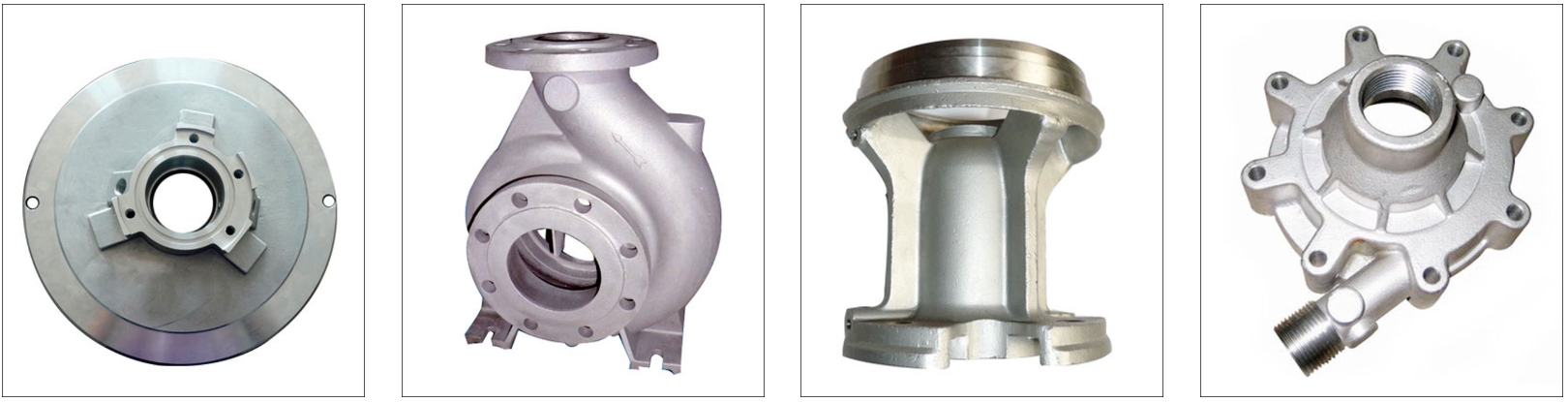
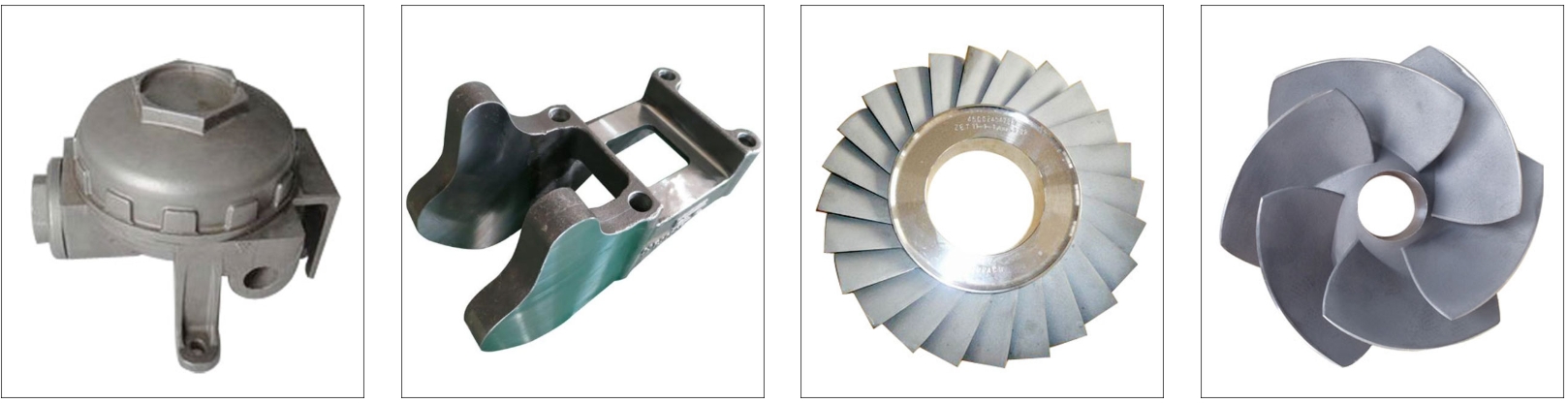