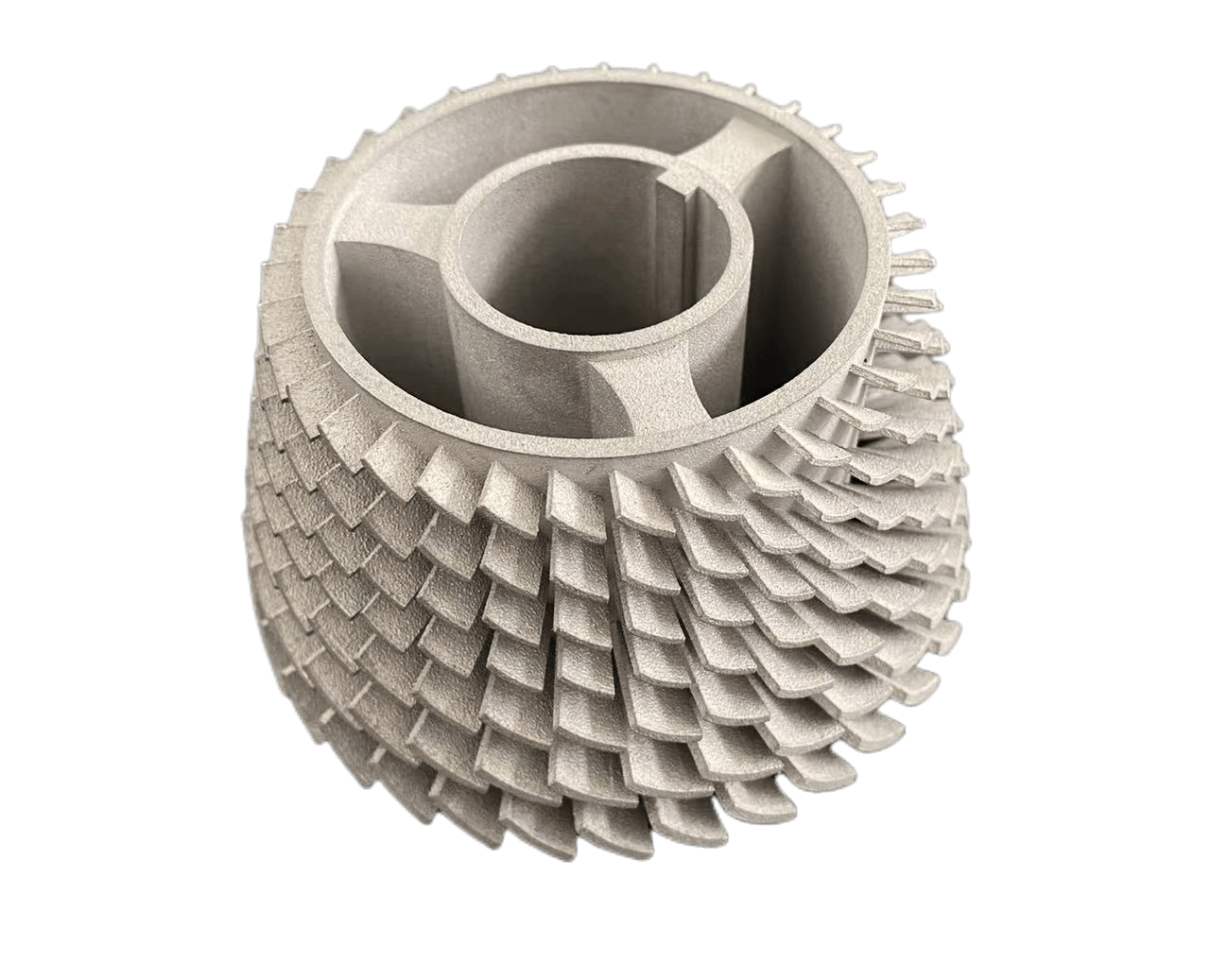
Jump to Section
→ Capabilities
→ Compare Material Properties
→ Material Options
→ Post-Processing
→ Why Metal 3D Printing?
Direct metal laser sintering (DMLS) is an industrial metal 3D printing process that builds fully functional metal prototypes and production parts in 7 days or less. A range of metals produce final parts that can be used for end-use applications.
Metal 3D printing technology is commonly used for:
- Prototyping in production-grade materials
- Complex geometries
- Functional, end-use parts
- Reducing metal components in an assembly
Metal 3D Printing Capabilities
Our basic guidelines for metal 3D printing include important design considerations to help improve part manufacturability, enhance cosmetic appearance, and reduce overall production time.
Max Dimensions | |||||||||||
---|---|---|---|---|---|---|---|---|---|---|---|
*At this time, Inconel 718 and Aluminum are the only materials available on our large format, X Line machine |
Layer Thickness | ||||||||||||
---|---|---|---|---|---|---|---|---|---|---|---|---|
*At this time, Inconel 718 and Aluminum are the only materials available on our large format, X Line machine |
Minimum Feature Size |
---|
Metal 3D Printing Tolerances
For well-designed parts, tolerances in the X/Y dimension of ±0.003 in. (0.075mm) for first inch plus 0.1% of nominal length. (0.001mm/mm), and Z dimension tolerances of ±0.006 in. for first inch plus 0.1% of nominal length, can typically be achieved. Note that tolerances may change depending on part geometry.
*At this time, Inconel 718 and Aluminum are the only materials available on our large format, X Line machine.
Surface Finishes | ||||||||||
---|---|---|---|---|---|---|---|---|---|---|
|
Compare Material Properties
Metals
US | |||||||||||||||||||||||||||||||||||||||||||||||||||||||||||||||||||||||||||||||||||||||||||||||||||||||||||||
---|---|---|---|---|---|---|---|---|---|---|---|---|---|---|---|---|---|---|---|---|---|---|---|---|---|---|---|---|---|---|---|---|---|---|---|---|---|---|---|---|---|---|---|---|---|---|---|---|---|---|---|---|---|---|---|---|---|---|---|---|---|---|---|---|---|---|---|---|---|---|---|---|---|---|---|---|---|---|---|---|---|---|---|---|---|---|---|---|---|---|---|---|---|---|---|---|---|---|---|---|---|---|---|---|---|---|---|---|---|
20 μm = high resolution (HR) 30, 40, and 60 μm = normal resolution (NR) |
Metric | ||||||||||||||||||||||||||||||||||||||||||||||||||||||||||||||||||||||||||||||||||||||||||||||||||||||||||||||||||||
---|---|---|---|---|---|---|---|---|---|---|---|---|---|---|---|---|---|---|---|---|---|---|---|---|---|---|---|---|---|---|---|---|---|---|---|---|---|---|---|---|---|---|---|---|---|---|---|---|---|---|---|---|---|---|---|---|---|---|---|---|---|---|---|---|---|---|---|---|---|---|---|---|---|---|---|---|---|---|---|---|---|---|---|---|---|---|---|---|---|---|---|---|---|---|---|---|---|---|---|---|---|---|---|---|---|---|---|---|---|---|---|---|---|---|---|---|
20 μm = high resolution (HR) 30, 40, and 60 μm = normal resolution (NR) |
hese figures are approximate and dependent on a number of factors, including but not limited to, machine and process parameters. The information provided is therefore not binding and not deemed to be certified. When performance is critical, also consider independent lab testing of additive materials or final parts.
Metal 3D Printing Material Options
Below is our available metal alloys for 3D printing. Various heat treatments are available depending on material.
Stainless Steel (17-4 PH)
Stainless Steel 17-4 PH is a precipitation hardened stainless steel that is known for its hardness and corrosion resistance. If needing a stainless steel option, select 17-4 PH for its significantly higher tensile strength and yield strength, but recognize that it has far less elongation at break than 316L. Final parts built 17-4 PH receive vacuum solution heat treatment as well as H900 aging.
Primary Benefits
- Heat treated for full hardness and strength
- Corrosion resistance
Finishing Options
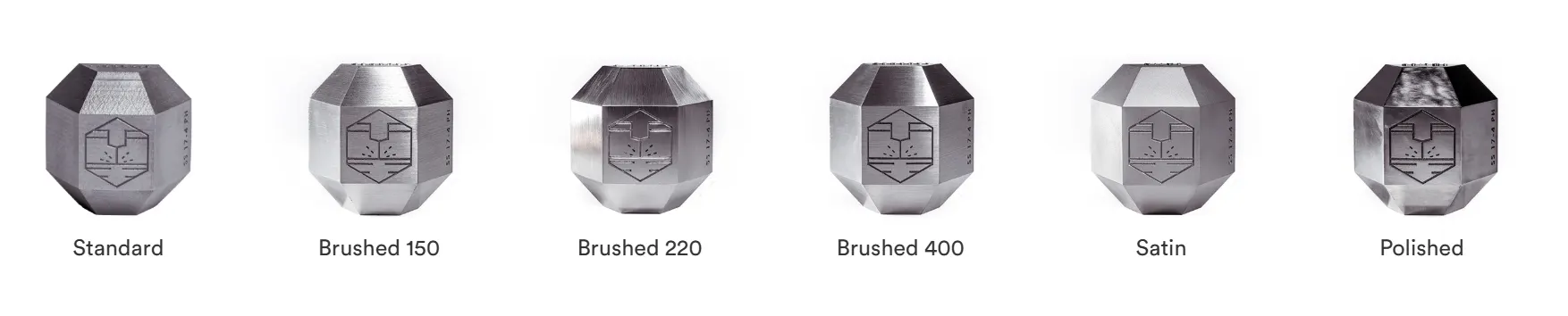
Stainless Steel (316L)
Choose 316L when stainless steel flexibility is needed; 316L is a more malleable material compared to 17-4 PH. Final parts built in 316L receive stress relief application.
Primary Benefits
- Heat treated for full hardness and strength
- Corrosion resistance
Primary Benefits
- Heat treated for full hardness and strength
- Corrosion resistance
Finishing Options
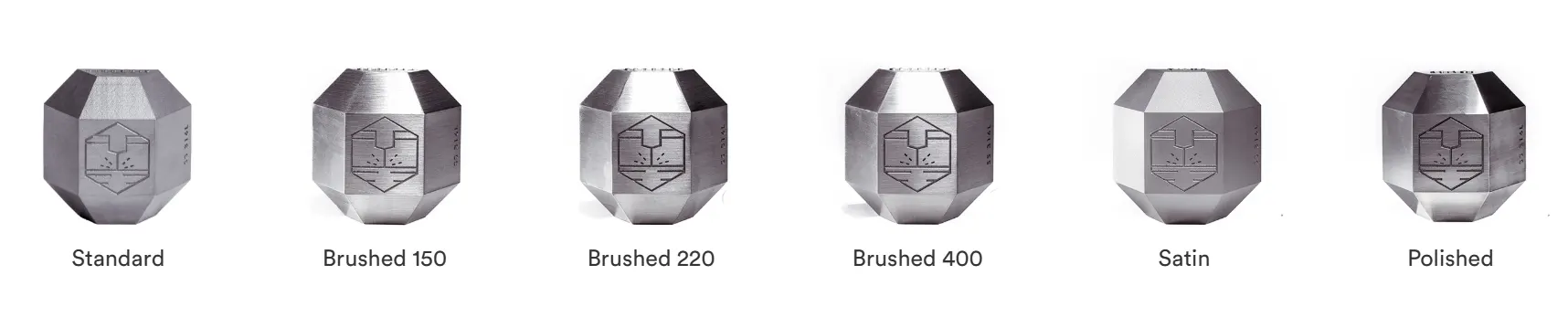
Aluminum (AlSi10Mg)
Aluminum (AlSi10Mg) is comparable to a 3000 series alloy that is used in casting and die casting processes. It has good strength -to-weight ratio, high temperature and corrosion resistance, and good fatigue, creep and rupture strength. AlSi10Mg also exhibits thermal and electrical conductivity properties. Final parts built in AlSi10Mg receive stress relief application.
Primary Benefits
- High stiffness and strength relative to weight
- Thermal and electrical conductivity
Custom Finishing Options

Inconel 718
Inconel is a high strength, corrosion resistant nickel chromium superalloy ideal for parts that will experience extreme temperatures and mechanical loading. Final parts built in Inconel 718 receive stress relief application. Solution and aging per AMS 5663 is also available to increase tensile strength and hardness.
Primary Benefits
- Oxidation and corrosion resistance
- High performance tensile, fatigue, creep, and rupture strength
Custom Finishing Options
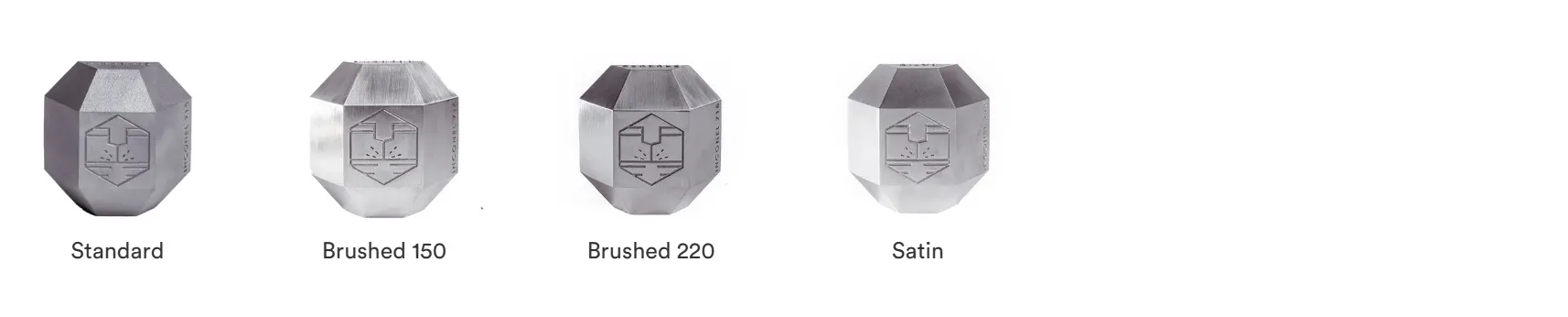
Cobalt Chrome (Co28Cr6Mo)
Cobalt Chrome (Co28Cr6Mo) is a superalloy comprised primarily of cobalt and chromium. It's high tensile strength and resistance to creep and corrosion makes it a good material choice for aerospace components and medical instrumentation.
Primary Benefits
- High performance tensile and creep
- Corrosion resistance
Custom Finishing Options
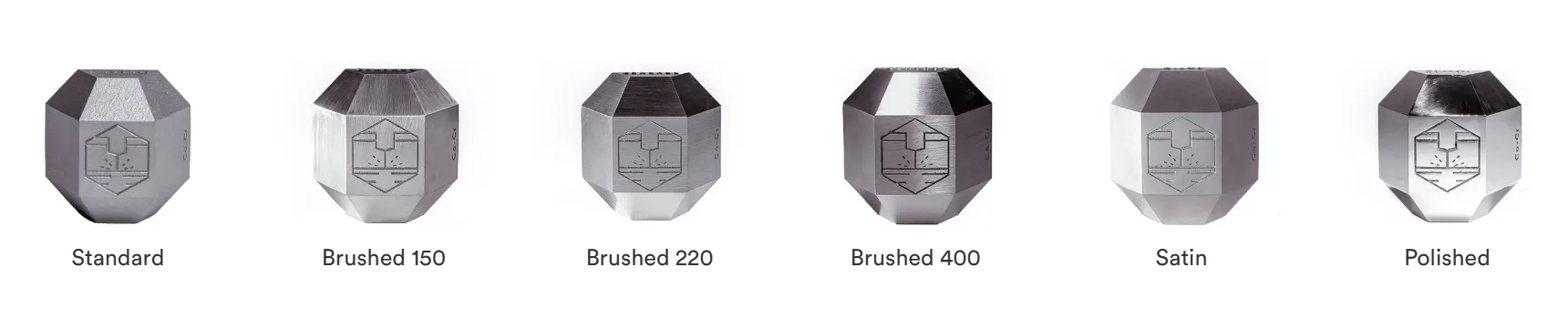
Titanium (Ti6Al4V)
Titanium (Ti6Al4V) is a workhorse alloy. When measured against Ti grade 23 annealed, the mechanical properties of Ti6Al4V are comparable to wrought titanium for tensile strength, elongation, and hardness.
Primary Benefits
- High stiffness and strength relative to weight
- High temperature and corrosion resistance
Custom Finishing Options
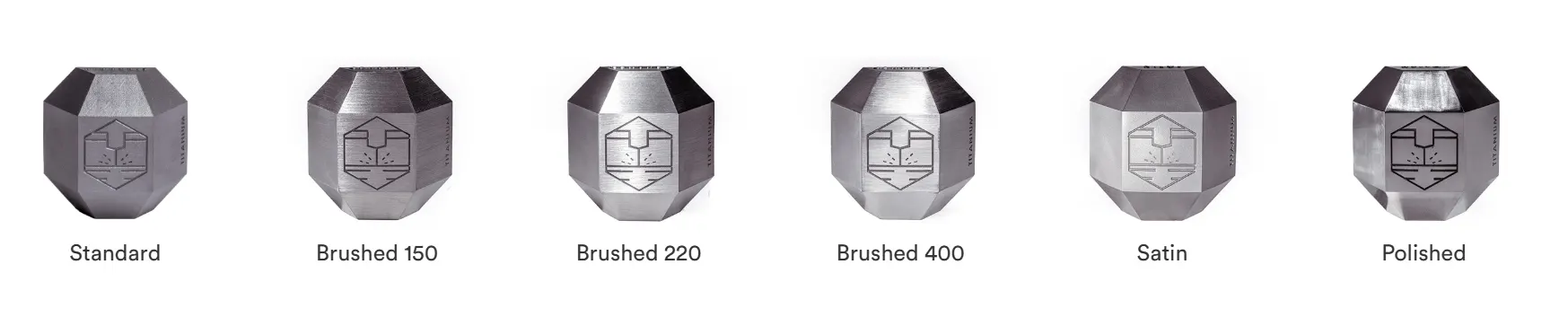
Post-Processing Capabilities for Metal 3D-Printed Parts
Improve strength, dimensional accuracy, and cosmetic appearance of final metal components with DMLS for production.
Surface Finishing
- 3- and 5-axis milling
- Turning
- Custom Finishing
- Brushed (150, 220, 400)
- Satin
- Polished
- Passivation
- Wire EDM
- Tapping and reaming
Heat Treatments
- Stress relief
- NADCAP heat treatment
- Hot isostatic pressing (HIP)
- Solution annealing
- Aging
Mechanical Testing
- Tensile
- Rockwell Hardness
Powder Analysis & Material
- Traceability
- Chemistry
- Particle size and distribution analysis
Why Use Metal 3D Printing?
See how metal additive manufacturing technology can be used to reduce components within an assembly, fabricate complex geometries, and ultimately save you time and costs.
How Does Metal 3D Printing Work?
The DMLS machine begins sintering each layer—first the support structures to the base plate, then the part itself—with a laser aimed onto a bed of metallic powder. After a cross-section layer of powder is micro-welded, the build platform shifts down and a recoater blade moves across the platform to deposit the next layer of powder into an inert build chamber. The process is repeated layer by layer until the build is complete.
When the build finishes, an initial brushing is manually administered to parts to remove a majority of loose powder, followed by the appropriate heat-treat cycle while still fixtured in the support systems to relieve any stresses. Parts are removed from the platform and support structures are removed from the parts, then finished with any needed bead blasting and deburring. Final DMLS parts are near 100 percent dense.
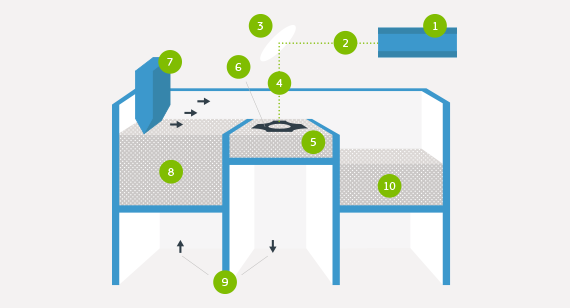
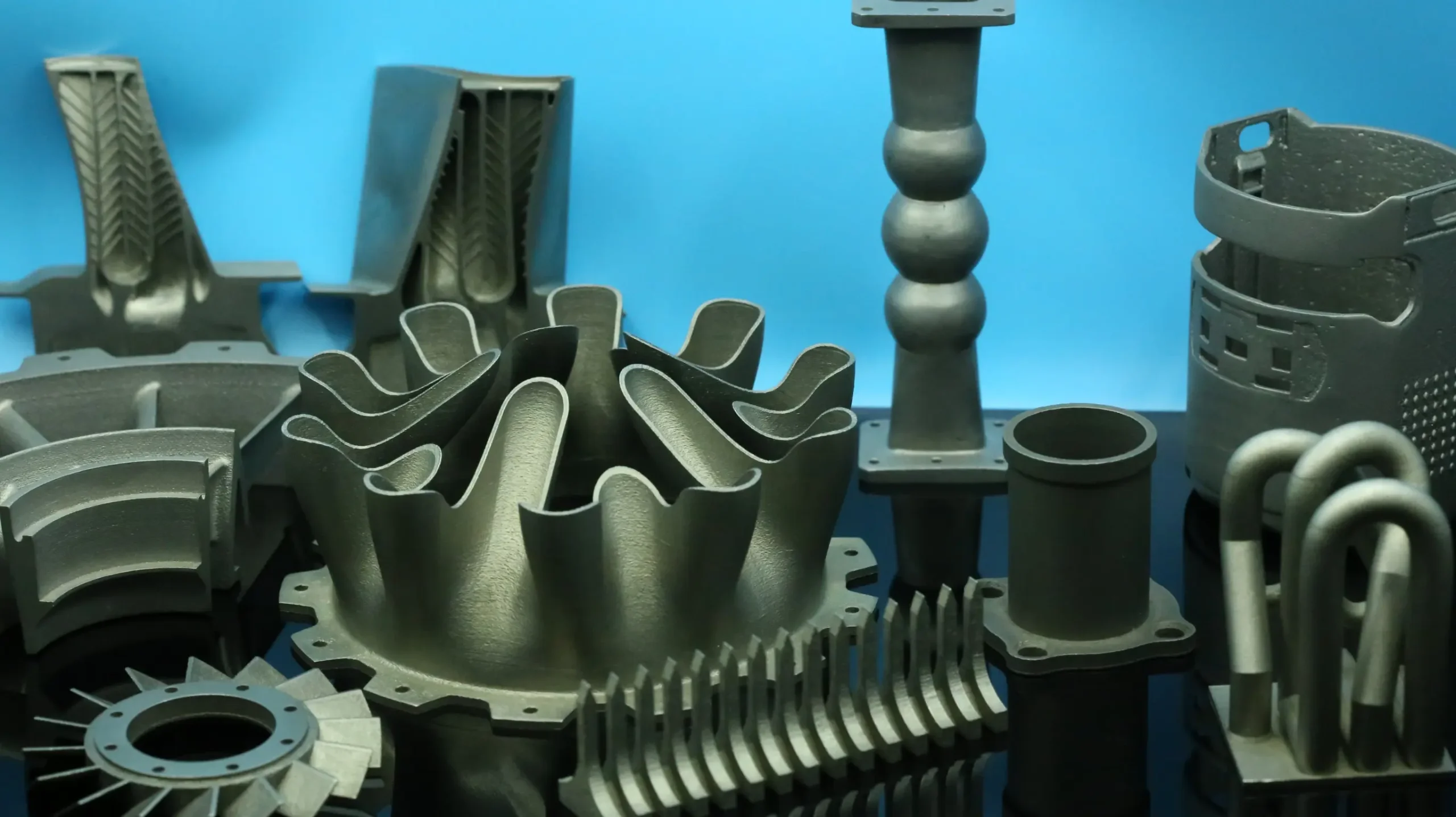
Large Format Metal 3D Printing
Our large format 3D printers can build metal parts as large as 31.5 in. x 15.7 in. x 19.7 in. in Aluminum and Inconel. Large, 3D-printed parts are often used in industrial settings, aerospace applications, automotive, and energy.