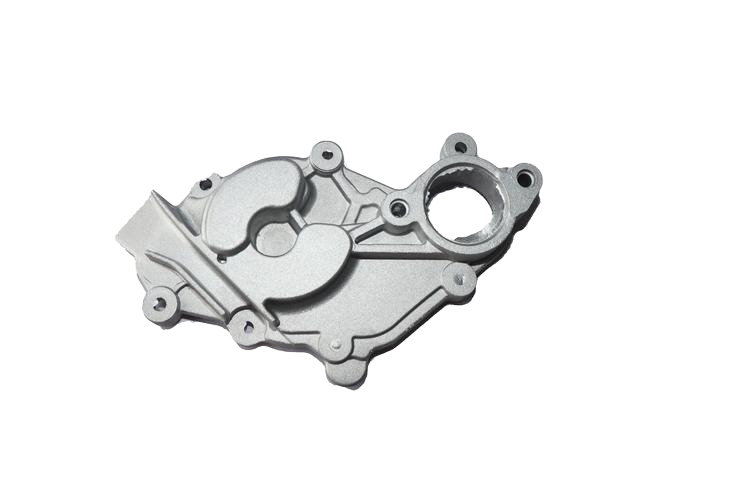
What is die casting mold manufacturing?
Die-casting materials, die-casting machines, and molds are the three essential elements in die-casting production, and none of them can be omitted. The so-called die-casting process refers to the organic and comprehensive application of these three elements to stably, rhythmically, and efficiently produce qualified castings—even high-quality ones—that meet the requirements of drawings or agreements in terms of appearance, internal quality, and dimensions.
A die-casting mold is a tool for casting metal parts, and it is a tool used to complete the die-casting process on a special die-casting and forging machine. The basic die-casting process is as follows: first, molten metal is poured into the mold cavity at a low or high speed. The mold has a movable cavity surface, and pressure forging is performed during the cooling process of the molten metal. This not only eliminates the shrinkage and looseness defects of the blank but also makes the internal structure of the blank achieve broken grains in a forged state, thereby significantly improving the comprehensive mechanical properties of the blank.
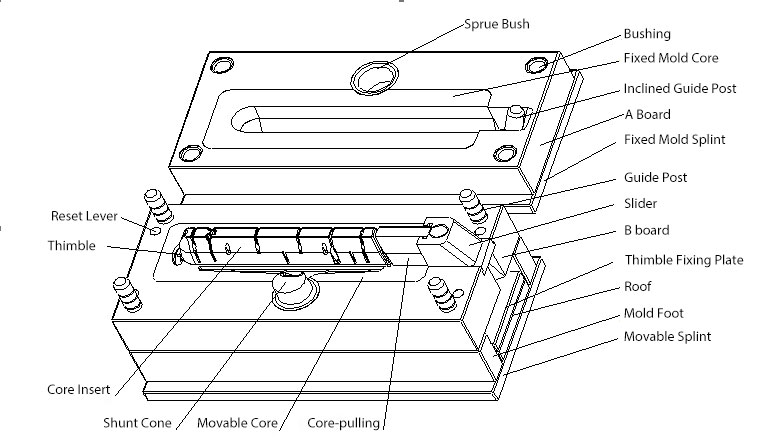
Components of Die-Casting Molds
Die Casting Mold Design Process
Advantages of Die Casting Mold Manufacturing and Molding Services
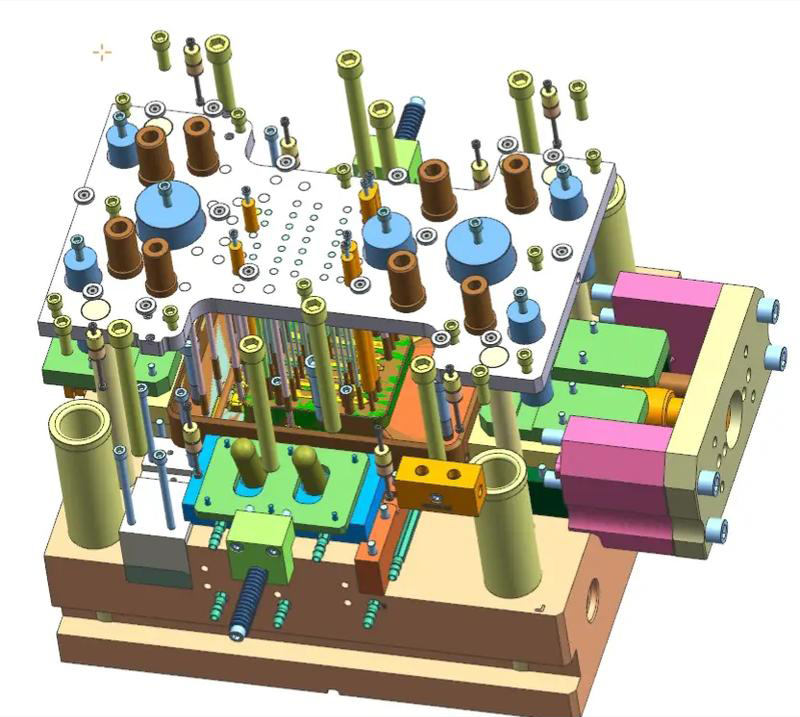
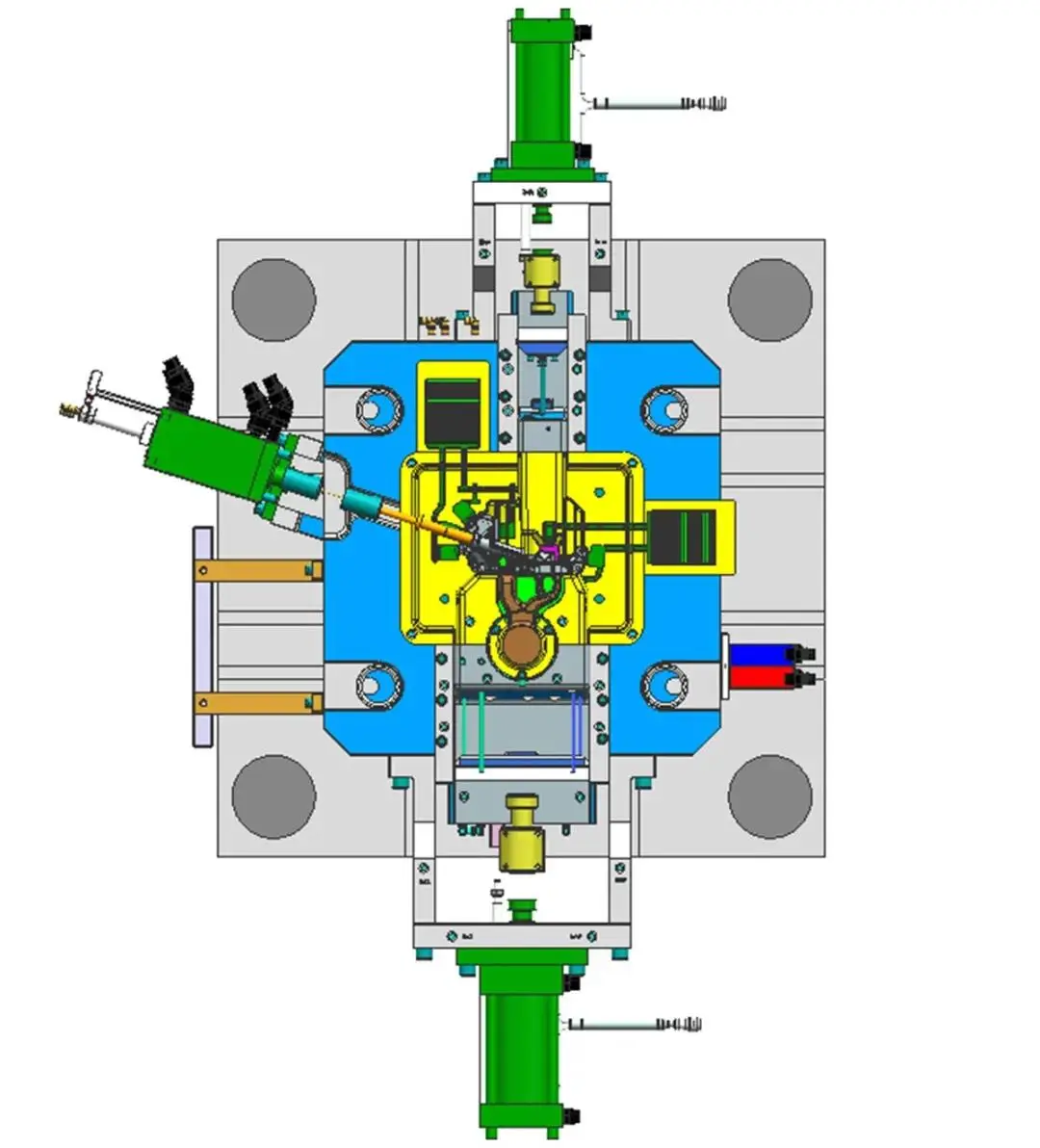
Applications
Online Mold Manufacturing Services
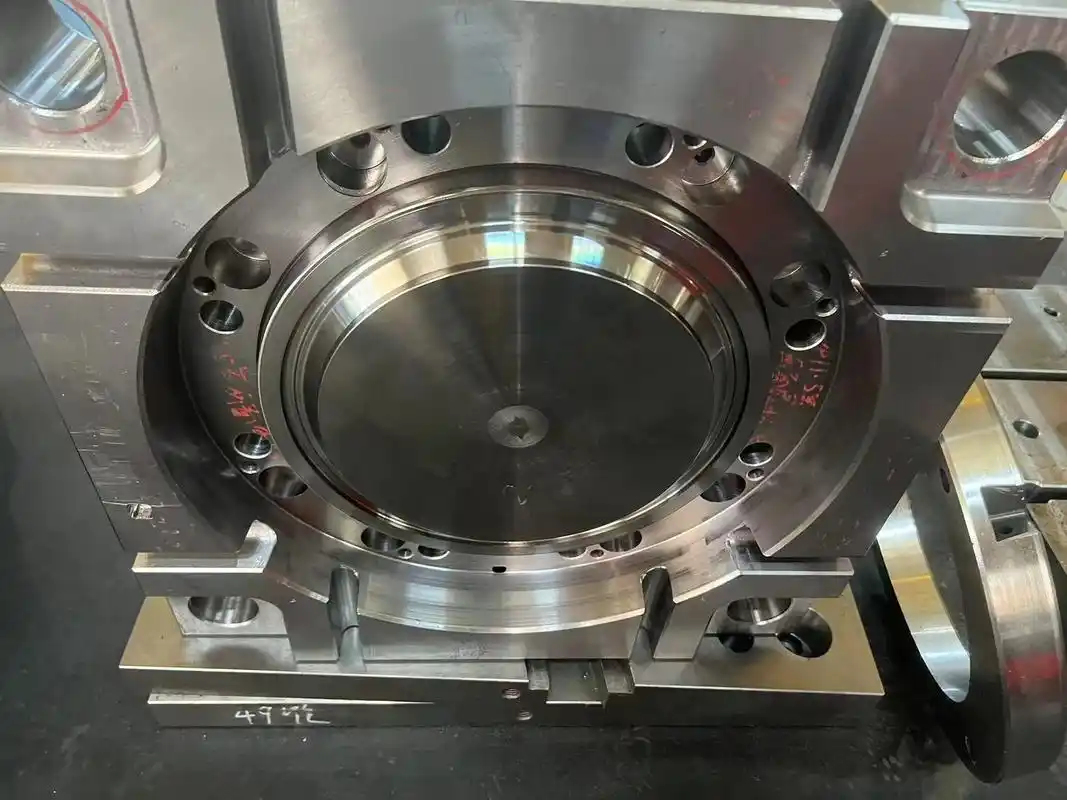
Die Casting Mold Design and Manufacturing: How to Make Die Casting Molds
Global Die-Casting Mold Manufacturing Services
Seven Typical Processes of Die-Casting Manufacturing:
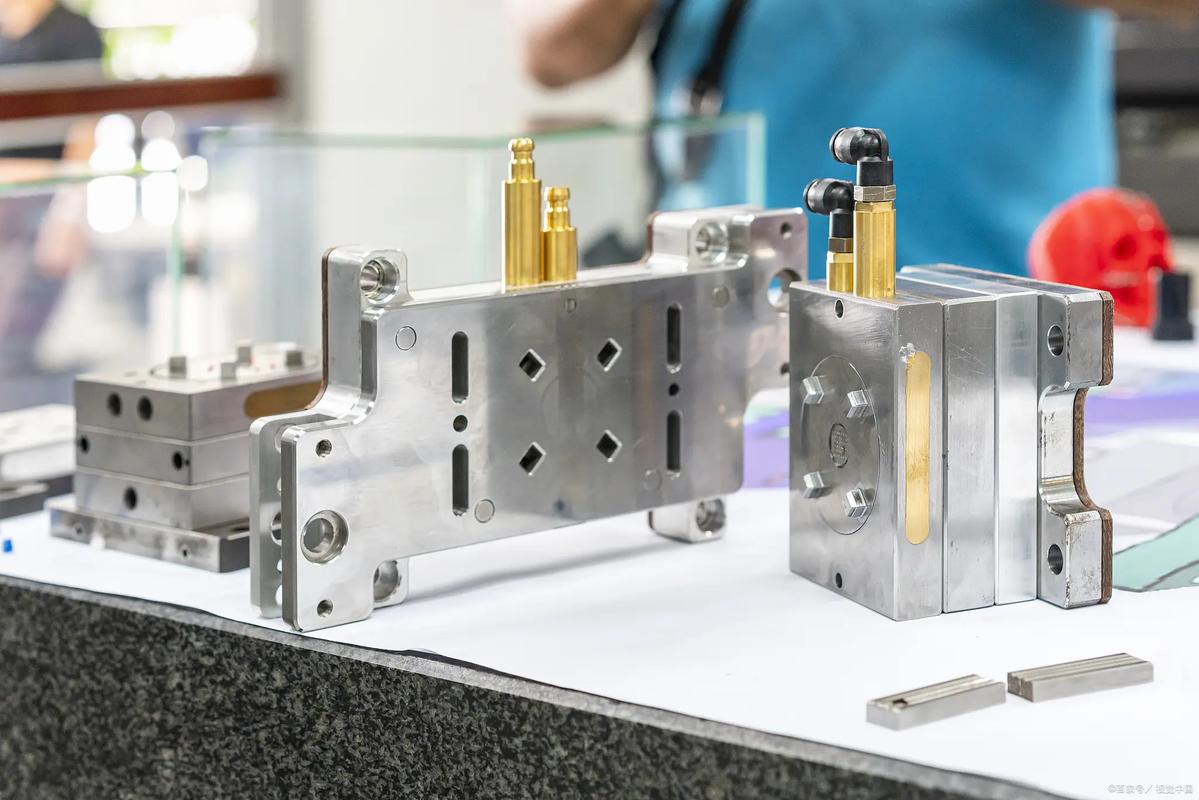
Design for Manufacturability Content
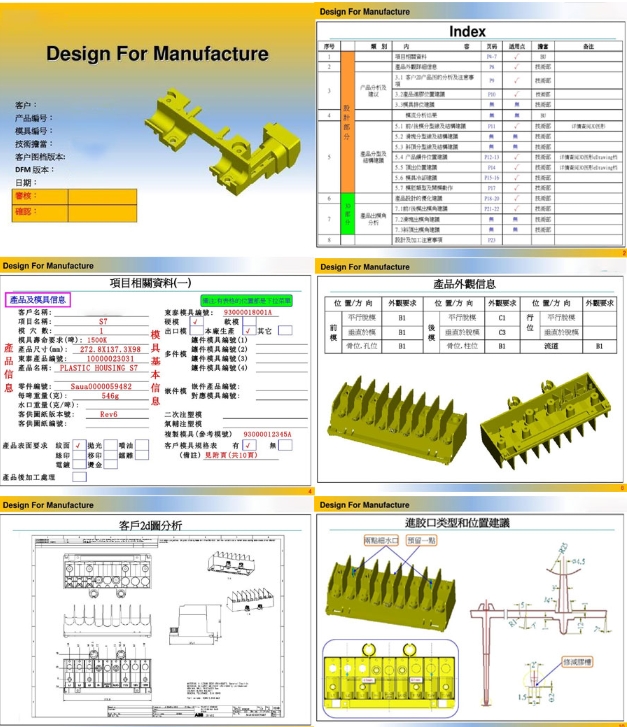
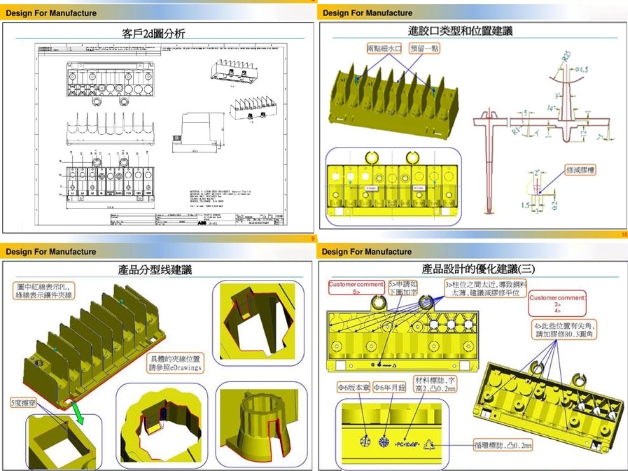
Whether you only need product design drawings, mold manufacturing, or precise specifications for the final die castings, XS can meet your needs with competitive prices, excellent efficiency, and top-tier customer service.