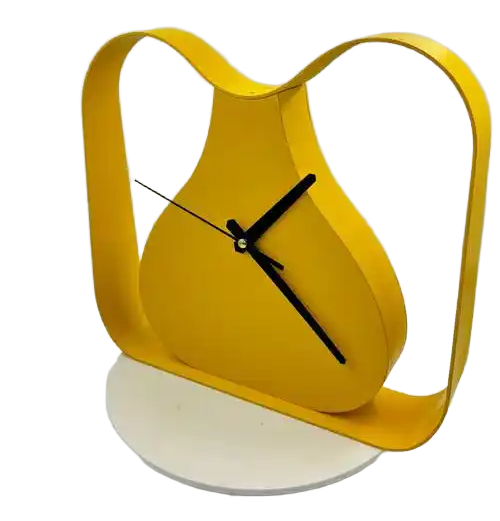
Jump to Section
→ Capabilities
→ Materials
→ XS 3D Printers
→ About XS 3D Printing
XS is an industrial 3D printing process that builds multi-material prototypes with flexible features and complex parts with intricate geometries in as fast as 1 day. A range of hardnesses (durometers) are available, which work well for components with elastomeric features like gaskets, seals, and housings.
Common applications for XS 3D printing:
- prototyping designs for overmolding or silicone rubber parts
- combining two colors or durometers into a single part
- simulating elastomers or flexible parts
XS Design Guidelines and Capabilities
Our basic guidelines for XS include important design considerations to help improve part manufacturability, enhance cosmetic appearance, and reduce overall production time.
US | Metric | |
Maximum Part Size | 19.3 in. x 15.4 in. x 7.9 in. | 490mm x 390mm x 200mm |
Layer Thickness | 0.00118 in. | 30 microns |
Minimum Feature Size | 0.012 in. | 0.3mm |
Minimum Freestanding Wall, Hole, or Channel Size | 0.030 in. | 0.76mm |
Tolerances for XS: For well-designed parts, tolerances of ±0.005 (0.1mm) for the first inch plus 0.1% of nominal length can typically be achieved. Note that tolerances may change depending on part geometry.
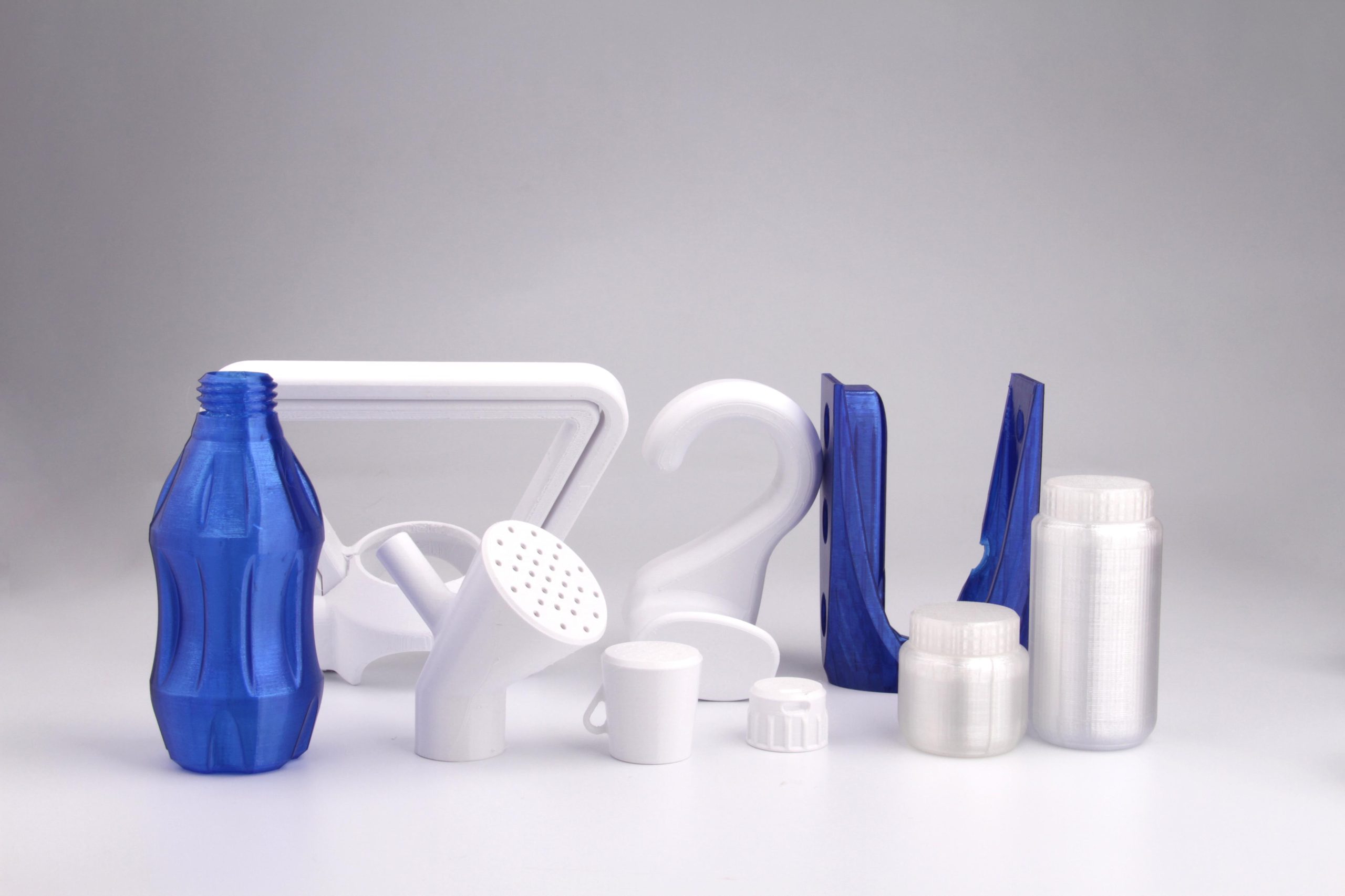
XS Material Options
XS provides the ability to choose a desired hardness or combine material properties into a single build, which makes it ideal for prototyping overmolding parts. Shore A hardnesses of 30A, 40A, 50A, 60A, 70A, 85A, 95A, and rigid are available in these colors:
- Digital Clear/Translucent
- Digital Black
- Digital White
Compare PolyJet Material Properties
US | ||||||||||||||||||||||||||||||||||||
---|---|---|---|---|---|---|---|---|---|---|---|---|---|---|---|---|---|---|---|---|---|---|---|---|---|---|---|---|---|---|---|---|---|---|---|---|
|
Metric | ||||||||||||||||||||||||||||||||||||
---|---|---|---|---|---|---|---|---|---|---|---|---|---|---|---|---|---|---|---|---|---|---|---|---|---|---|---|---|---|---|---|---|---|---|---|---|
|
These figures are approximate and dependent on a number of factors, including but not limited to, machine and process parameters. The information provided is therefore not binding and not deemed to be certified. When performance is critical, also consider independent lab testing of additive materials or final parts.
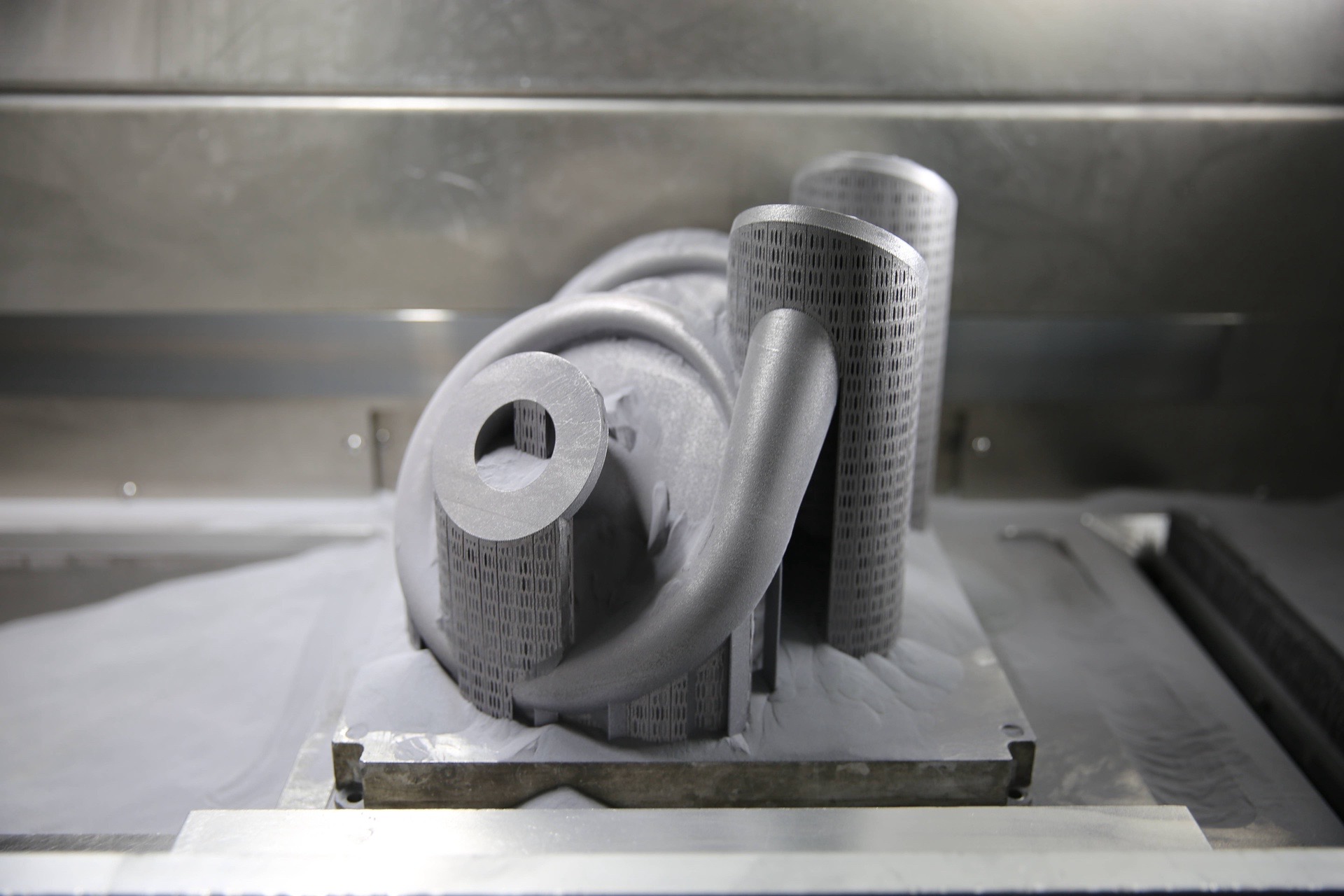
Our XS 3D Printers
We use multiple additive machines that offer large build sizes, accurate parts, and quick production times. Our XS equipment consists of:
- Objet260 Connex3
- Objet350 Connex3
How Does XS 3D Printing Work?
The XS process begins by spraying small droplets of liquid photopolymers in layers that are instantly UV cured. Voxels (three-dimensional pixels) are strategically placed during the build, which allow for the combination of both flexible and rigid photopolymers know as digital materials. Each voxel has a vertical thickness equal to the layer thickness of 30 microns. The fine layers of digital materials accumulate on the build platform to create accurate 3D-printed parts.
Each XS part is completely coated in support material during the build, which ultimately is removed by hand using a pressurized water stream and a chemical solution bath. No post-curing is required after the manufacturing process.