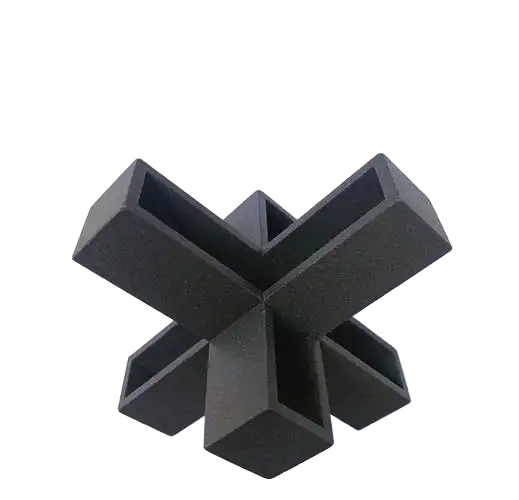
Jump to Section
→ Capabilities
→ Materials
→ Surface Finishes
→ SLS 3D Printers
→ About Selective Laser Sintering
Selective laser sintering (SLS) is an industrial 3D printing process that produces accurate prototypes and functional production parts in as fast as 1 day. Multiple nylon-based materials and a thermoplastic polyurethane (TPU) are available, which create highly durable final parts that require heat resistance, chemical resistance, flexibility, or dimensional stability. With SLS 3D printing, no support structures are required making it easy to nest multiple parts into a single build and an economical solution for when higher volumes of 3D-printed parts are required.
Common uses for selective laser sintering are:
- jigs and fixtures
- housings
- snap fits and living hinges
Why Use SLS?
See how SLS uses actual thermoplastic and elastomeric materials to produce parts with good mechanical properties. Final parts can be used to test future injection molding designs or as functional, end-use components.
Vapor Smoothing is Here!
Vapor smoothing is now available for select 3D-printed nylon parts. The process eliminates rough surfaces and leaves a glossy, aesthetic finish on parts.
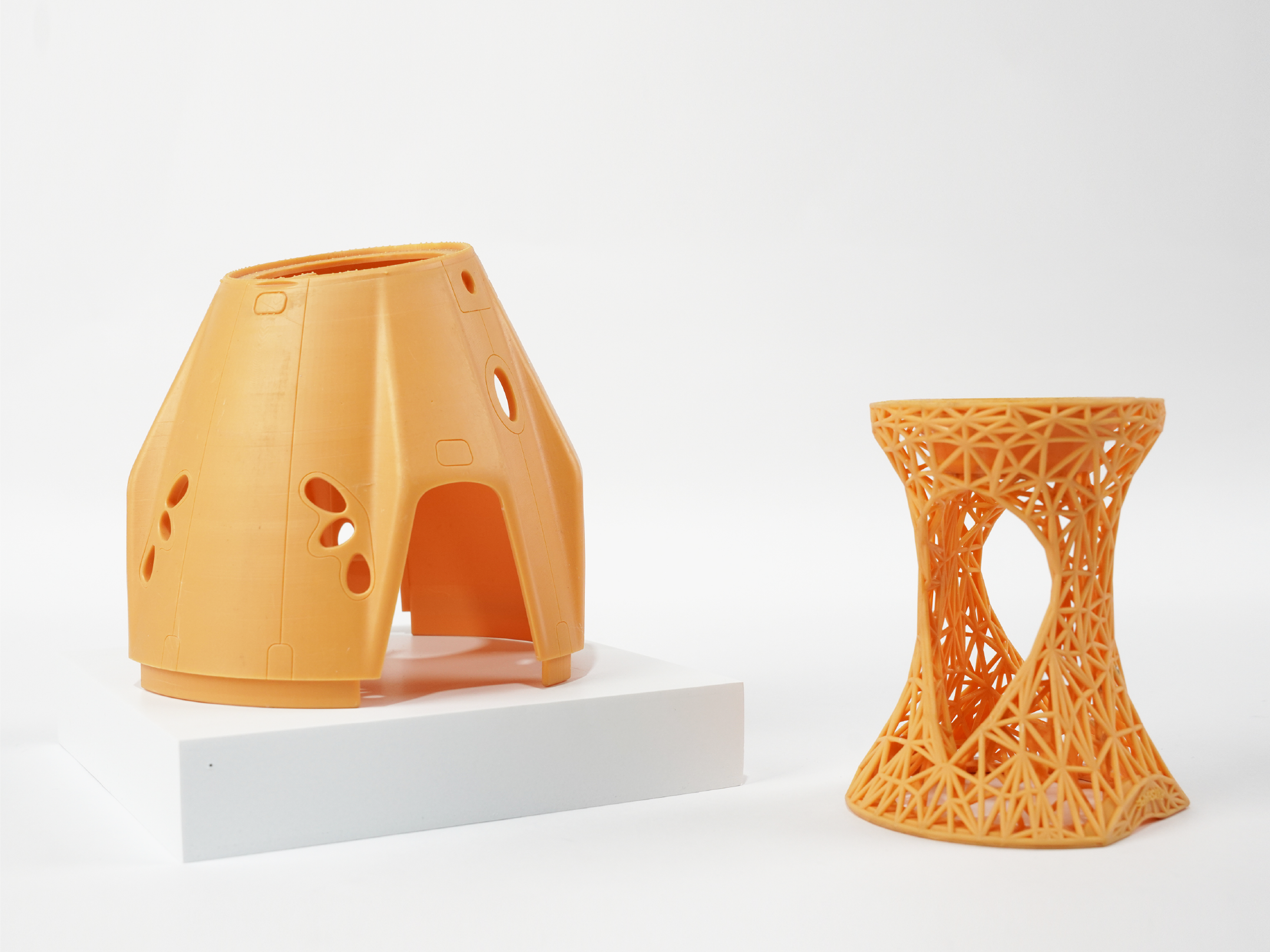
Design Guidelines for Selective Laser Sintering (SLS)
Our basic guidelines for selective laser sintering include important design considerations to help improve part manufacturability, enhance cosmetic appearance, and reduce overall production time.
- Max Dimensions
- Layer Thickness / Resolution
- Wall Thickness
- Minimum Feature Size
- Tolerances
- Warpage
- Surface Finish Options
Max Dimensions | ||||||||||||
---|---|---|---|---|---|---|---|---|---|---|---|---|
|
Layer Thickness / Resolution | ||||||
---|---|---|---|---|---|---|
| ||||||
|
Wall Thickness | |||||
---|---|---|---|---|---|
|
Minimum Feature Size | ||||||||
---|---|---|---|---|---|---|---|---|
|
SLS Tolerances
For well-designed parts, tolerances of ±0.010 in. (0.25mm) plus 0.1% of nominal length can typically be achieved. Note that tolerances may change depending on part geometry.
SLS Part Warpage
Larger part sizes (>7 in.) and parts with thin features are the most susceptible to warp. We recommend maintaining a uniform thickness of 0.125 in. (3.175mm) to ensure stability.
Surface Finish Options | ||||||||
---|---|---|---|---|---|---|---|---|
|
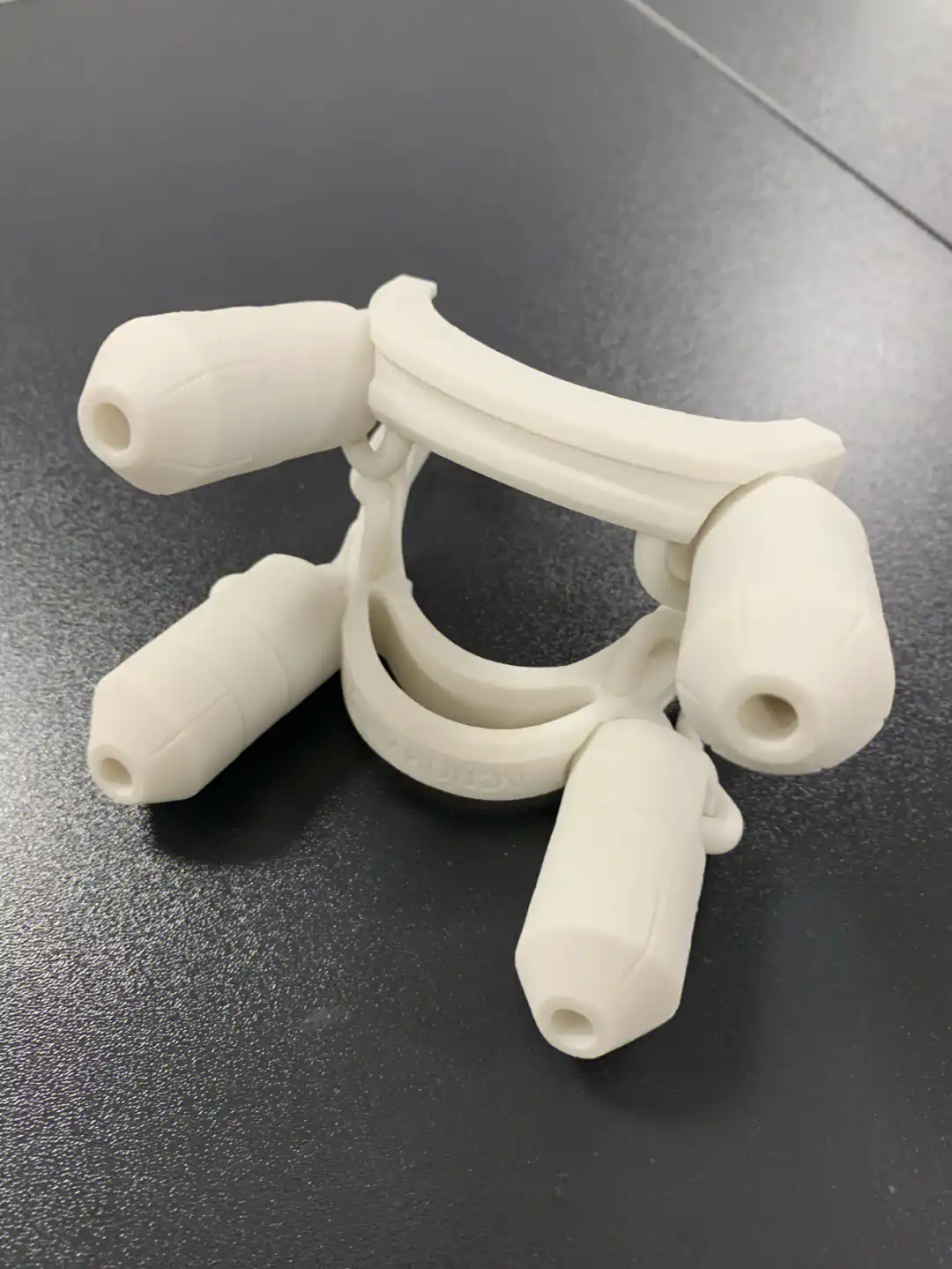
Selective Laser Sintering (SLS) Materials
Primary Benefits
Highest elongation at break of all additively manufactured nylons Uniform deep-black color that showcases features and provides a clean appearance
Primary Benefits
Highly isotropic mechanical propertiesEconomical material choice
Primary Benefits
Economical material choice Strength and stiffness
Primary Benefits
SustainabilityDurability
Versatility
Primary Benefits
Highest stiffness of all additively manufactured nylonsTemperature resistance
Primary Benefits
Long-term wear resistance Increased stiffness
Primary Benefits
Chemical resistanceDurable, low weight material
Primary Benefits
High elongation at breakFlexibility
Compare Material Properties
US | |||||||||||||||||||||||||||||||||||||||||||||
---|---|---|---|---|---|---|---|---|---|---|---|---|---|---|---|---|---|---|---|---|---|---|---|---|---|---|---|---|---|---|---|---|---|---|---|---|---|---|---|---|---|---|---|---|---|
|
Metric | |||||||||||||||||||||||||||||||||||||||||||||
---|---|---|---|---|---|---|---|---|---|---|---|---|---|---|---|---|---|---|---|---|---|---|---|---|---|---|---|---|---|---|---|---|---|---|---|---|---|---|---|---|---|---|---|---|---|
|
These figures are approximate and dependent on a number of factors, including but not limited to, machine and process parameters. The information provided is therefore not binding and not deemed to be certified. When performance is critical, also consider independent lab testing of additive materials or final parts.
Surface Finish for SLS Parts
Surface finish on SLS parts is typically rougher than other 3D printing technologies—it can range from 100-250 RMS. We also bead blasts the majority of customers’ parts to remove loose powder and create a smooth matte finish. Vapor smoothing is a post-processing option available for PA11 Black parts, which will result in surface finish roughness between 64 – 100 μin RA.
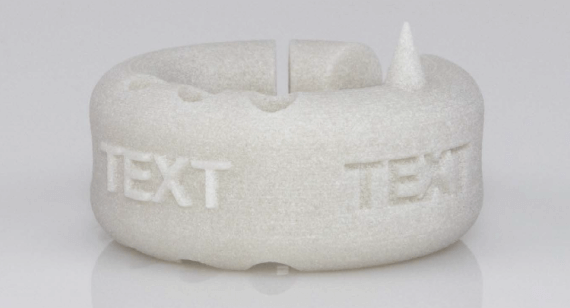
Material: PA12 40% Glass-Filled (PA614-GS)
Resolution: Normal (0.004 in. layer thickness)
Finish: Standard
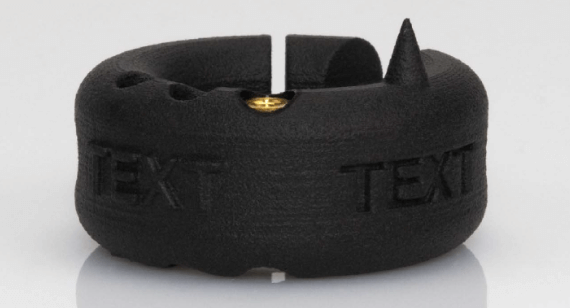
Material: PA11 Black (PA850)
Resolution: Normal (0.004 in. layer thickness)
Finish: Standard
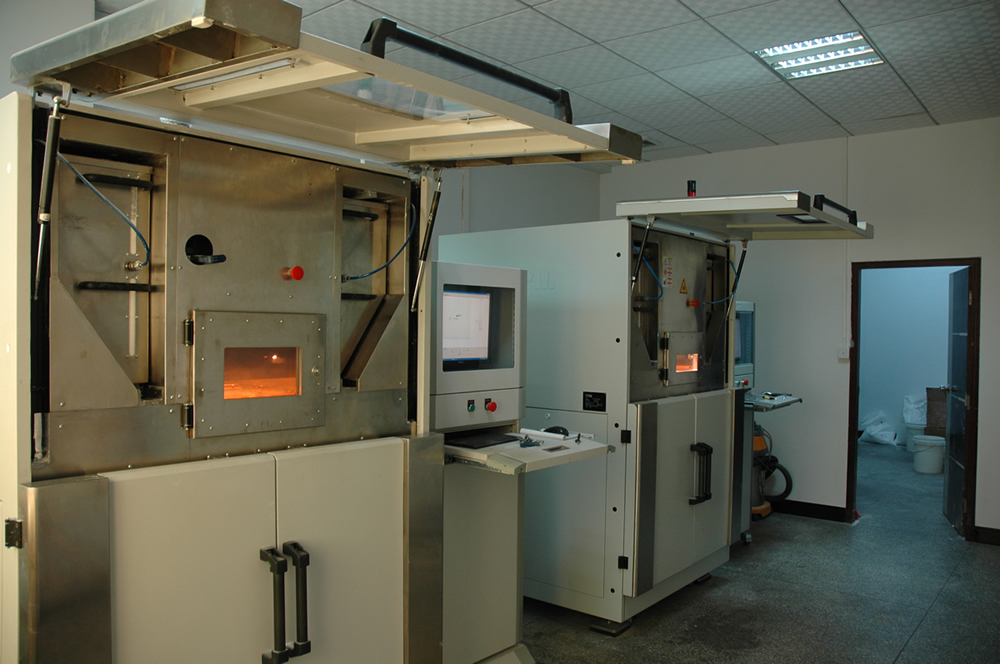
Our SLS 3D Printers
Our SLS equipment includes sPro140 machines, which have the world’s largest sintering build volume, and feature fully digital high-speed scanning systems, unparalleled process consistency, and closed systems for powder blending and delivery for reliable part quality. We also use sPro60 machines, which allow for multiple materials and high throughput.
How Does SLS 3D Printing Work?
The SLS machine begins sintering each layer of part geometry into a heated bed of nylon-based powder. After each layer is fused, a roller moves across the bed to distribute the next layer of powder. The process is repeated layer by layer until the build is complete.
When the build finishes, the entire powder bed with the encapsulated parts is moved into a breakout station, where it is raised up, and parts are broken out of the bed. An initial brushing is manually administered to remove a majority of loose powder. Parts are then bead blasted to remove any of the remaining residual powder before ultimately reaching the finishing department.
Tour Our 3D Printing Facility
Take a quick tour through our additive manufacturing facility in North Carolina, one of the largest 3D printing operations in the world, to see how we build high-quality prototypes and fully functional end-use components and assemblies.