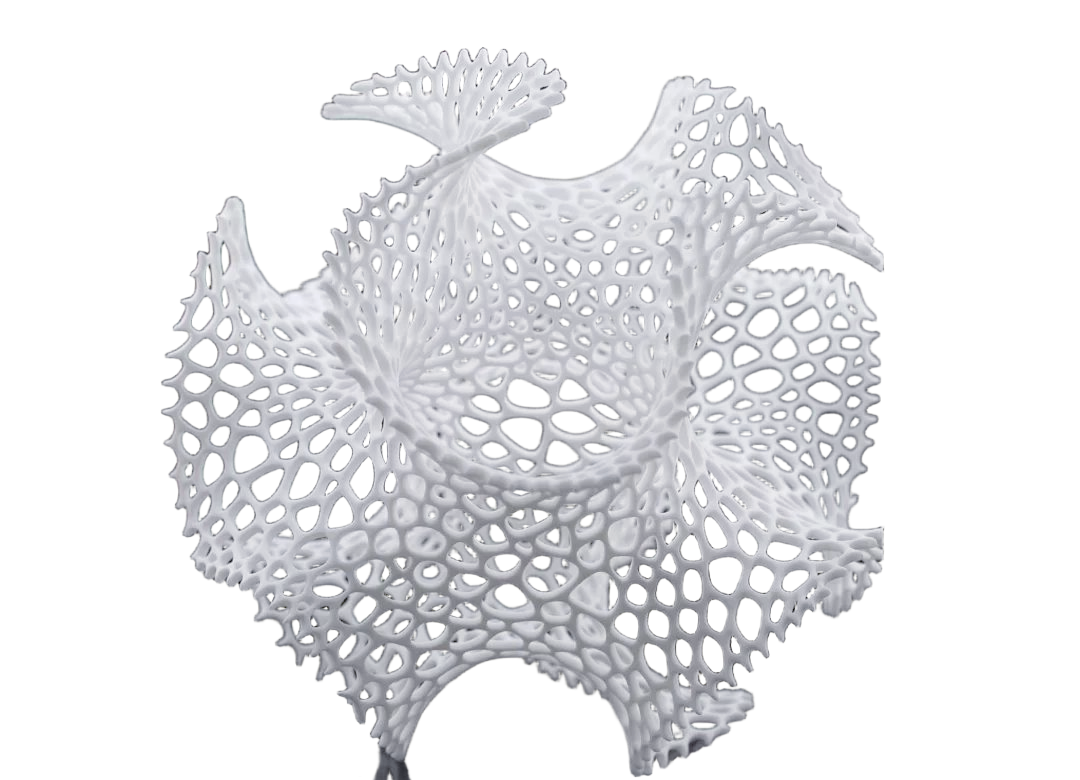
Jump to Section
→ Capabilities
→ SLA Materials
→ Compare SLA Material Properties
→ Surface Finishes
→ Post-Processing
→ Our SLA 3D Printers
→ Why SLA 3D Printing
What is Stereolithgraphy?
Stereolithography (SLA) is a 3D printing process used to create concept models, cosmetic prototypes, and complex parts with intricate geometries. It's an additive manufacturing technology that forms parts by curing thermoset resin with a UV laser. A wide selection of materials, extremely high feature resolutions, and quality surface finishes are possible with SLA.
SLA 3D printing is primarily used for:
- parts requiring high accuracy and features as small as 0.002 in.
- good surface quality for cosmetic prototypes
- form and fit testing
SLA Design Guidelines and Capabilities
Our basic guidelines for stereolithography include important design considerations to help improve part manufacturability, enhance cosmetic appearance, and reduce overall production time.
Max Part Size | |||||||||||
---|---|---|---|---|---|---|---|---|---|---|---|
|
Layer Thickness | |||||||||||
---|---|---|---|---|---|---|---|---|---|---|---|
|
Minimum Feature Size | |||||||||||
---|---|---|---|---|---|---|---|---|---|---|---|
|
Minimum Wall Thickness | |||||||||||
---|---|---|---|---|---|---|---|---|---|---|---|
|
Minimum Hole Size | |||||||||||
---|---|---|---|---|---|---|---|---|---|---|---|
|
SLA Tolerances
For well-designed parts, tolerances in the X/Y dimension of ±0.002 in. (0.05mm) for first inch plus 0.1% of nominal length. (0.001mm/mm), and Z dimension tolerances of ±0.005 in. for first inch plus 0.1% of nominal length, can typically be achieved. Note that tolerances may change depending on part geometry.*Available for the following materials: ABS-Like White and Gray, ABS-Like Translucent/Clear, and PC-Like Translucent/Clear
Compare Material Properties
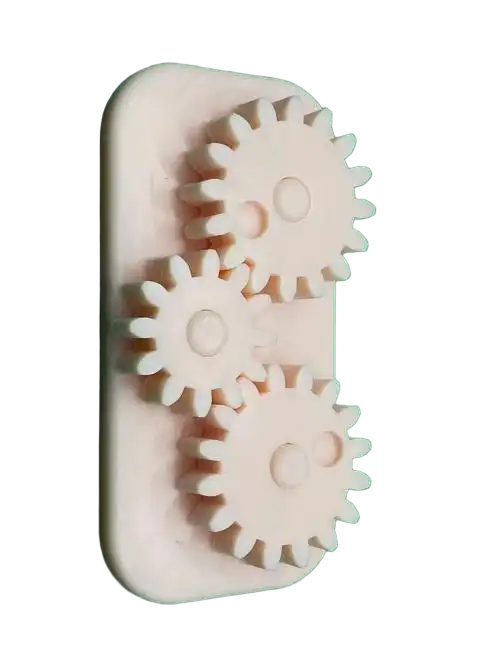
SLA Material Options
Primary Benefits
Durable, general purpose resinAccommodates extra-large parts
Primary Benefits
Durable, general purpose resinHighest HDT of the ABS-like SLA resins
Primary Benefits
Low moisture absorptionGlossy cosmetic appearance
Primary Benefits
Lowest moisture absorption of SLA resinsFunctional transparency
Primary Benefits
Produces highest resolution partsIdeal for extra-small parts
Primary Benefits
Semi-flexibleTranslucency
Primary Benefits
High elastic modulusHigher resistance to heated fluids
Primary Benefits
High stiffnessFunctional transparency
Primary Benefits
Stiffest SLA resinHighest HDT of SLA resins
Compare SLA Material Properties
US | |||||||||||||||||||||||||||||||||||||||||||||||||||||||
---|---|---|---|---|---|---|---|---|---|---|---|---|---|---|---|---|---|---|---|---|---|---|---|---|---|---|---|---|---|---|---|---|---|---|---|---|---|---|---|---|---|---|---|---|---|---|---|---|---|---|---|---|---|---|---|
*Properties listed are based on thermal cure |
Metric | |||||||||||||||||||||||||||||||||||||||||||||||||||||||
---|---|---|---|---|---|---|---|---|---|---|---|---|---|---|---|---|---|---|---|---|---|---|---|---|---|---|---|---|---|---|---|---|---|---|---|---|---|---|---|---|---|---|---|---|---|---|---|---|---|---|---|---|---|---|---|
*Properties listed are based on thermal cure |
These figures are approximate and dependent on a number of factors, including but not limited to, machine and process parameters. The information provided is therefore not binding and not deemed to be certified. When performance is critical, also consider independent lab testing of additive materials or final parts.
Surface Finish Options for SLA Parts
|
|
Unfinished | Dots, or standing"nibs," remain evident on the bottom of the part from the support structure remnants. Good for when fast lead times are required or cost is a factor |
Natural | Supported surfaces are sanded down to eliminate the support nibs. |
Standard | Supported surfaces are sanded, and the entire part is finely blasted for a consistent look. Note that the layers are still present. |
Custom | Soft-touch paint, clear part finishing, painting, masking, color matching, decals/graphic, and texture finishes are available. |
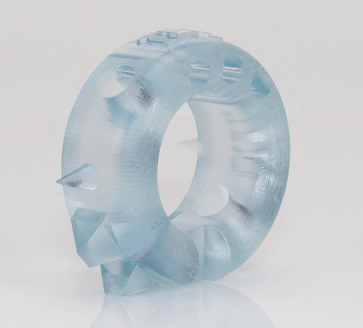
Material: ABS-like Translucent/Clear
Finish: Unfinished
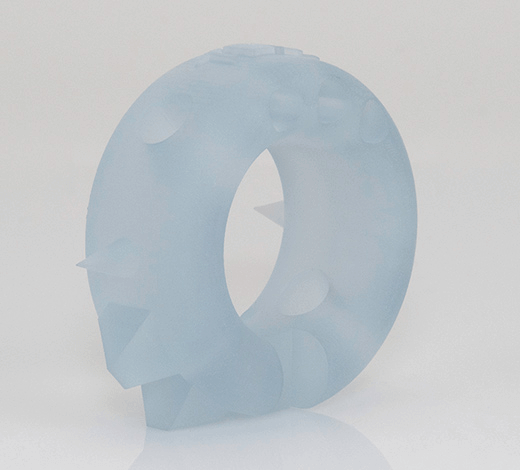
Material: ABS-like Translucent/Clear
Finish: Standard
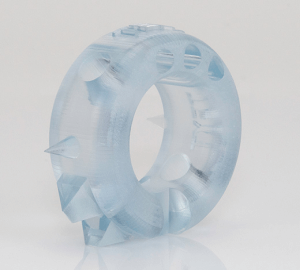
Material: ABS-like Translucent/Clear
Finish: Natural
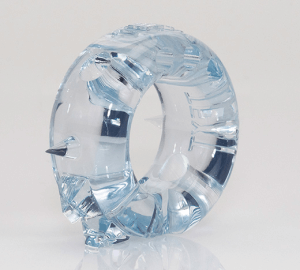
Material: ABS-like Translucent/Clear
Finish: Custom
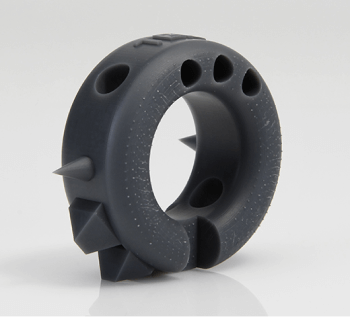
Material: MicroFine Gray™
Finish: Unfinished
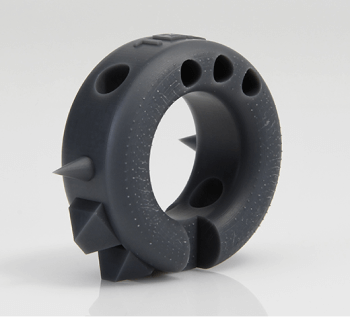
Material: MicroFine Gray™
Finish: Standard
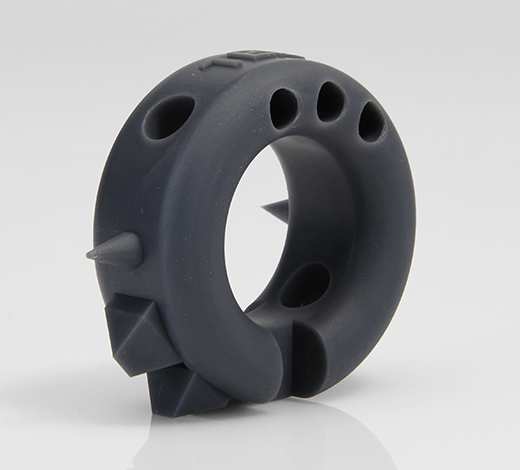
Material: MicroFine Gray™
Finish: Natural
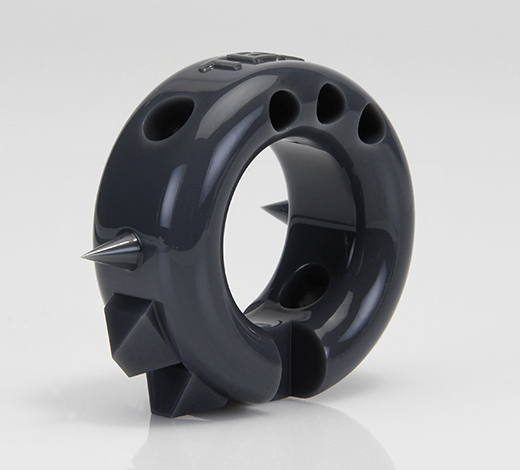
Material: MicroFine Gray™
Finish: Custom
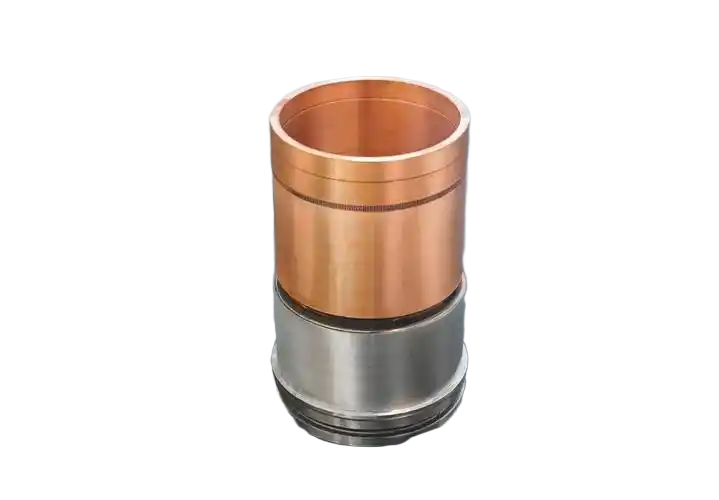
Metal Plating
Our metal-plating process for SLA coats a ceramic-filled PC-like material (Somos PerFORM) with a nickel that gives parts the look, feel, and strength of metal, but without the weight. The combination of the material’s strength, rigidity, and temperature resistance with nickel plating, takes strength, stiffness, and impact and temperature resistance to a degree previously unattainable in SLA parts.
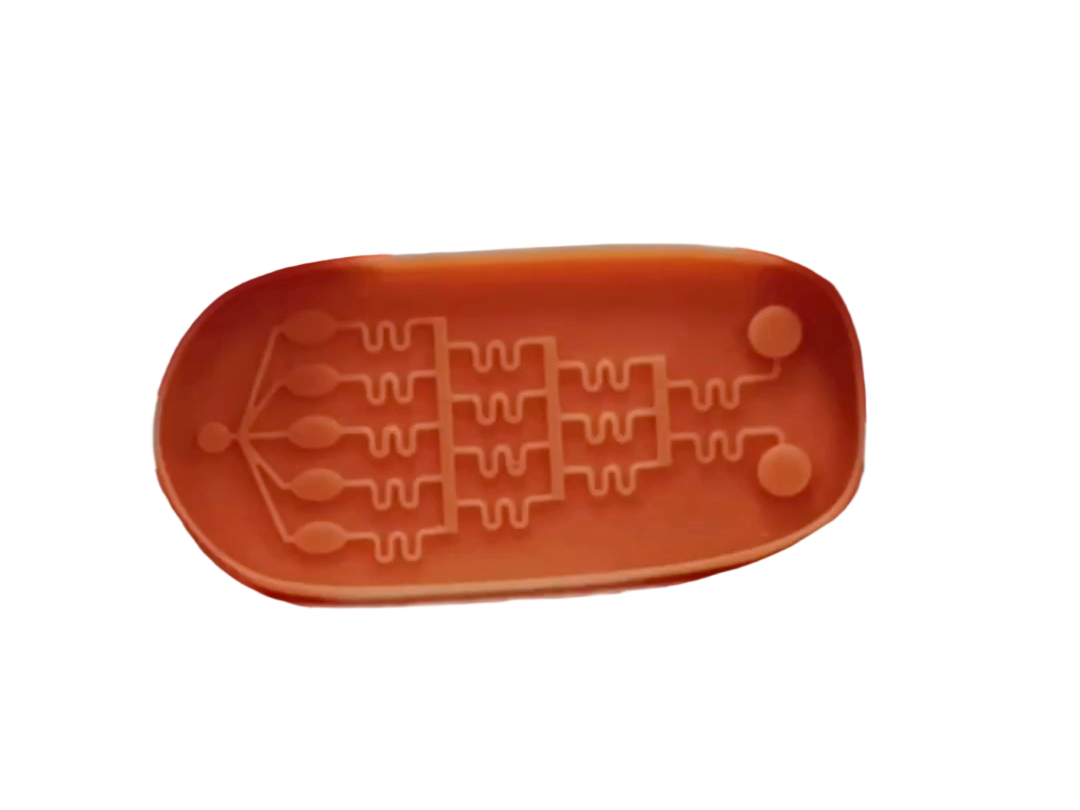
Microfluidics
Our microfluidic fabrication process is a modified form of high-resolution SLA that uses a clear ABS-like material (WaterShed XC 11122). Parts are resistance to water and humidity, and work well for lens and flow-visualization models.
Our SLA 3D Printers
Our stereolithography machines consists of Vipers, ProJets, and iPros. In high-resolution mode, Vipers and ProJets can make parts with extremely tiny features and crisp details, while in normal-resolution mode, they can build cost-effective parts very quickly.
iPros have extremely large build volumes at 29 in. by 25 in. by 21 in. (736mm by 635mm by 533mm), yet are still able to image highly detailed parts easily.
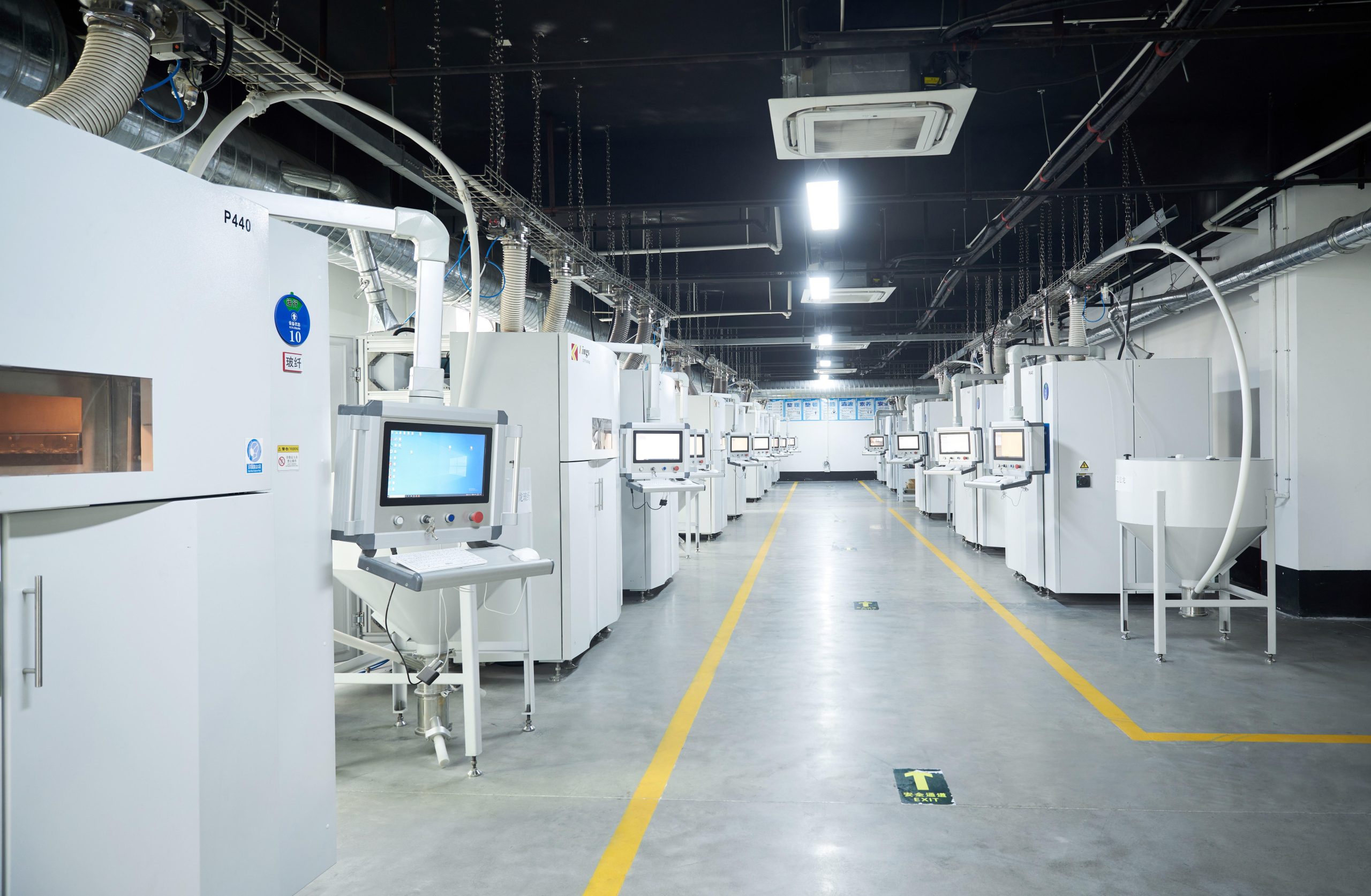
Why Use SLA?
Stereolithography (SLA) is an additive manufacturing process that can 3D print parts with small features, tight tolerance requirements, and smooth surface finishes.
How Does SLA 3D Printing Work?
The SLA machine begins drawing the layers of the support structures, followed by the part itself, with an ultraviolet laser aimed onto the surface of a liquid thermoset resin. After a layer is imaged on the resin surface, the build platform shifts down and a recoating bar moves across the platform to apply the next layer of resin. The process is repeated layer by layer until the build is complete.
Newly built parts are taken out of machine and into a lab where solvents are used to remove any additional resins. When the parts are completely clean, the support structures are manually removed. From there, parts undergo a UV-curing cycle to fully solidify the outer surface of the part. The final step in the SLA process is the application of any custom or customer-specified finishing. Parts built in SLA should be used with minimal UV and humidity exposure so they don’t degrade.